小さなバッグに注がれる、膨大な手仕事。
オリジナル刻印入りのカシメも完成し、糸や金具、ジッパーも到着した。準備は整った。いよいよサンプル製作に取り掛かる。
独立して5年目とは思えないほど充実した設備が揃う「GROOVER LEATHER」のファクトリー。新たな「OG-6」が誕生する空間としては、これ以上ない環境だ。
馬革の裁断から完成まで、一つひとつの工程を徳永氏、原山氏と共に確認&検証しながらの製作。丸一日の作業となったが、新たな「OG-6」のポテンシャルの高さをオガワ自身の目に焼き付けることができた貴重な時間となった。
Making of OG-6 new version

新たな「OG-6」に使うマテリアルは、新喜皮革が手掛けるフルベジタブルタンニン鞣しの馬革だ。創業1951年の馬革専業のタンナーで、原皮の鞣しから仕上げまで自社一貫生産する世界有数のタンナーだ。
染色は従来モデル同様、下地をブラウンに染めた「茶下地」。使い込み、表面が擦れることでブラウンが現れ、抜群の表情が楽しめる。
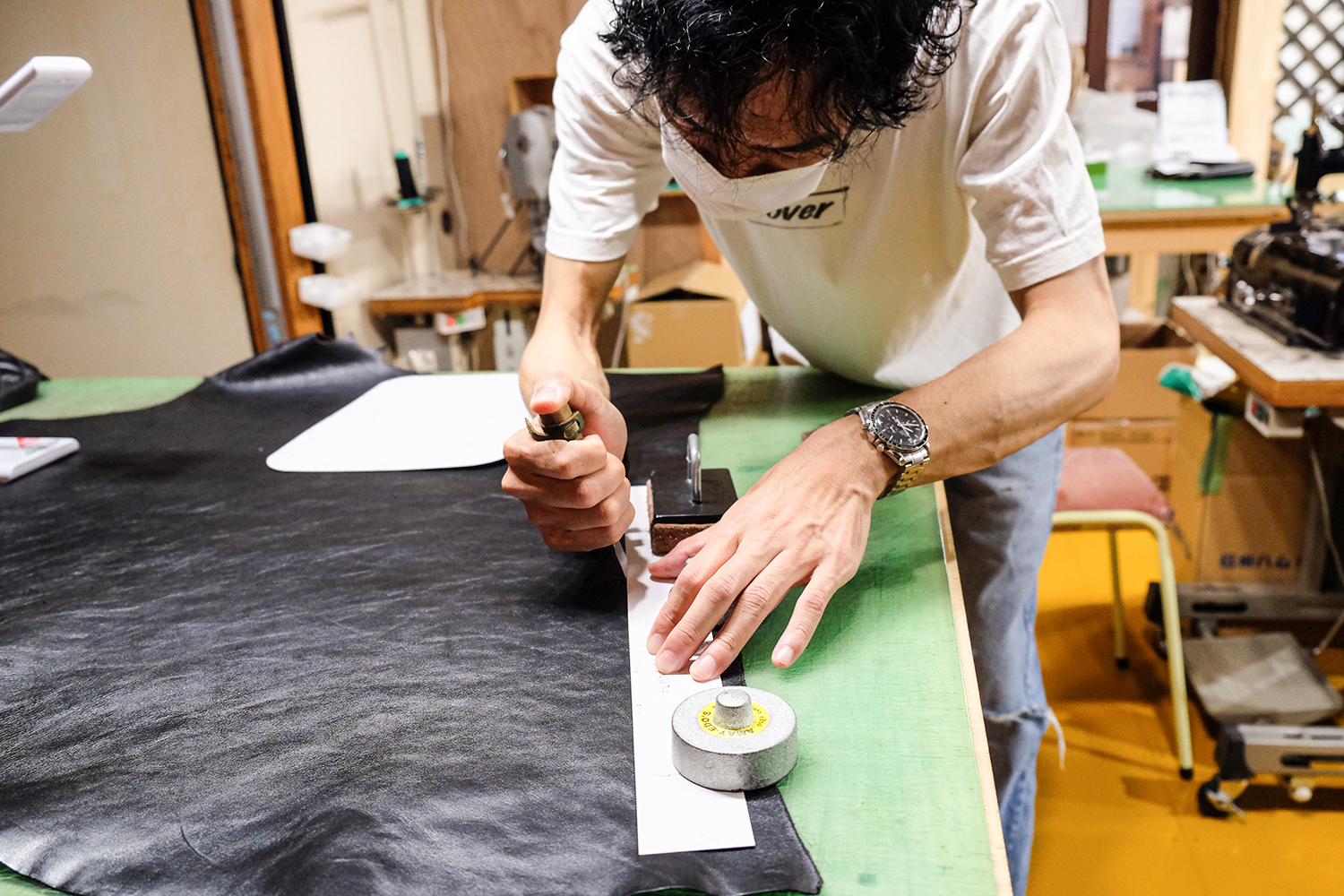
新たな「OG-6」は、よりコシ感の強い、カッチリとしたバッグを目指す。そのため、革の裁断には徹底的にこだわることにした。
ダイヤキルトを施すメインパネルに上質で綺麗な部位を使うことは当然だが、ボトムやサイドにも繊維の詰まったタフな部位を使うことにした。
ハンドルにもカッチリ感を出したいので、少し柔らかい革質の場合は芯材を挟み込む。ルーティン作業ではなく、馬革の個体差に合わせた製作を徳永氏にリクエストした。
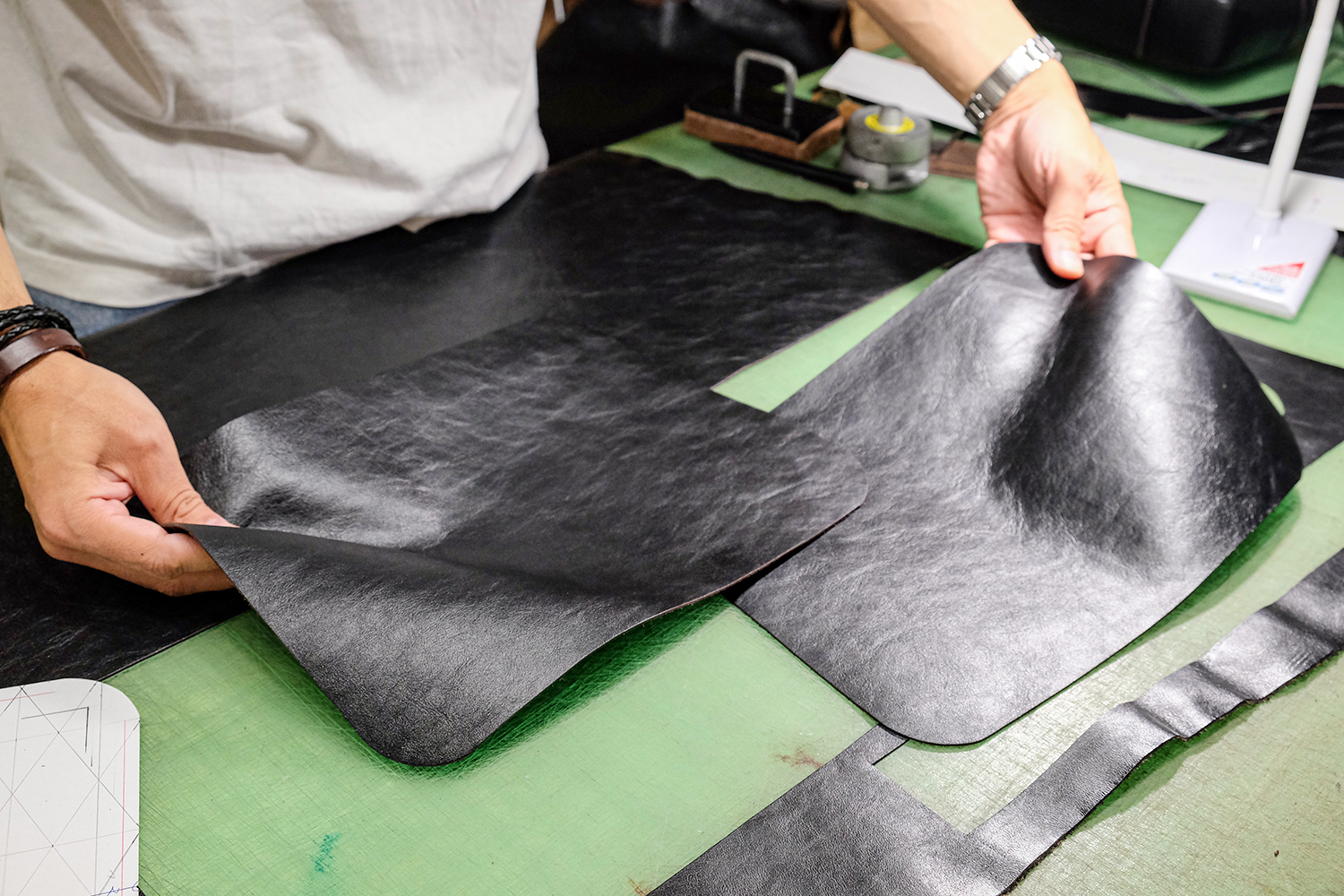
従来モデル同様、極上の馬革。しっかりとした厚みがあり、レザーJKTに使いたくなるほど美味しそうな革質だ。
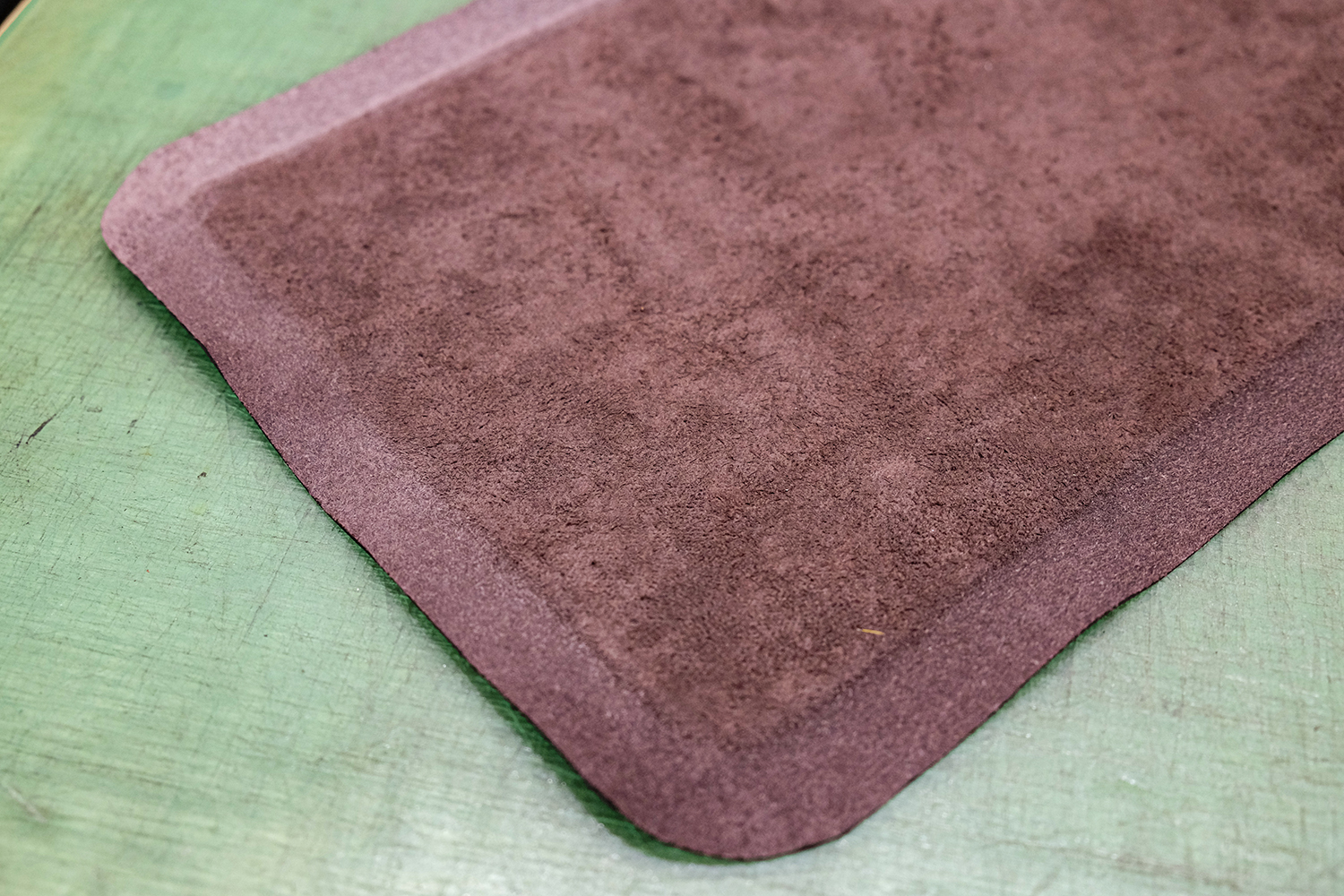
革漉き機で縫製箇所の厚みを整える。茶下地なので、馬革の床面はブラウン。床面からも品質の高さが伝わってくる。
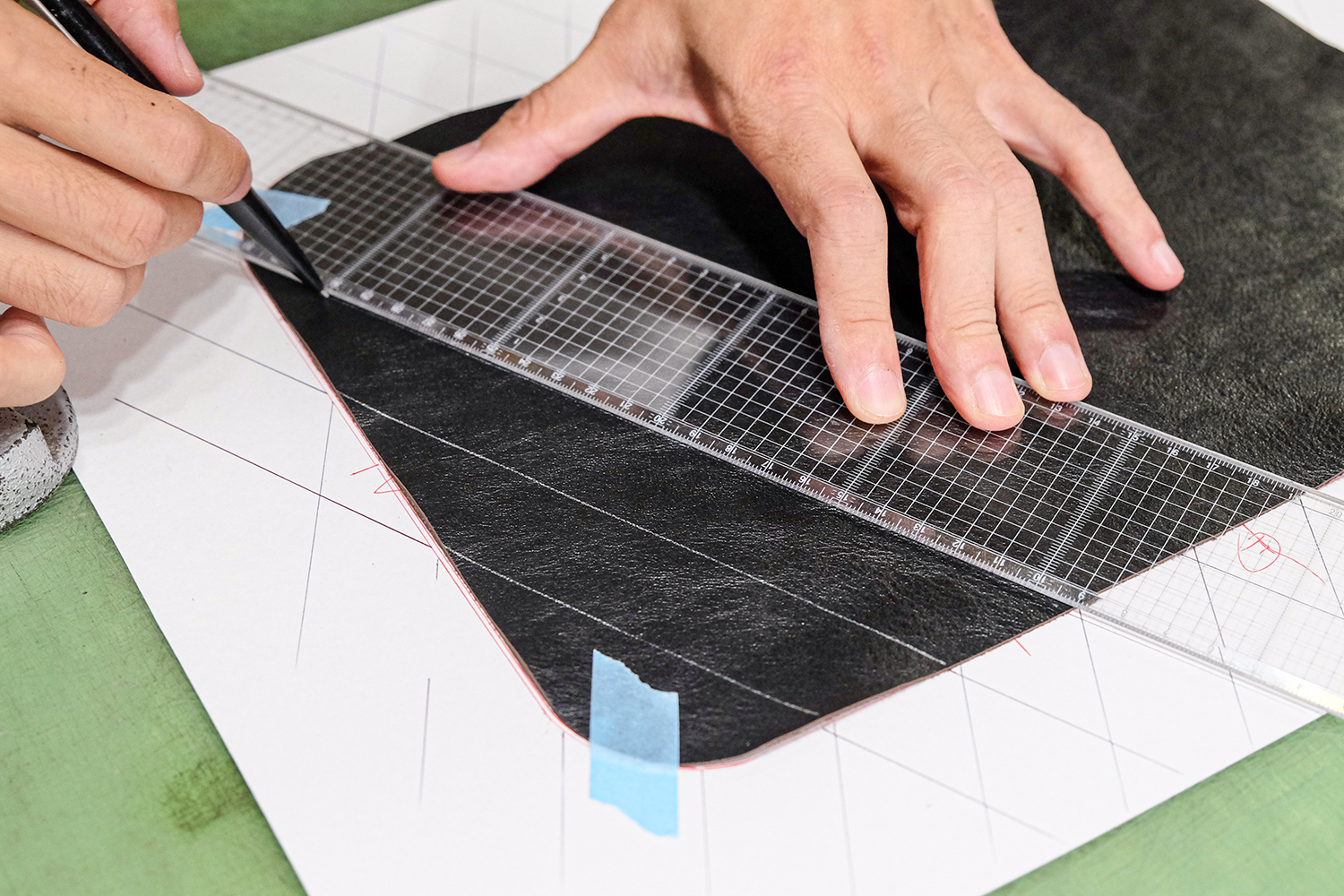
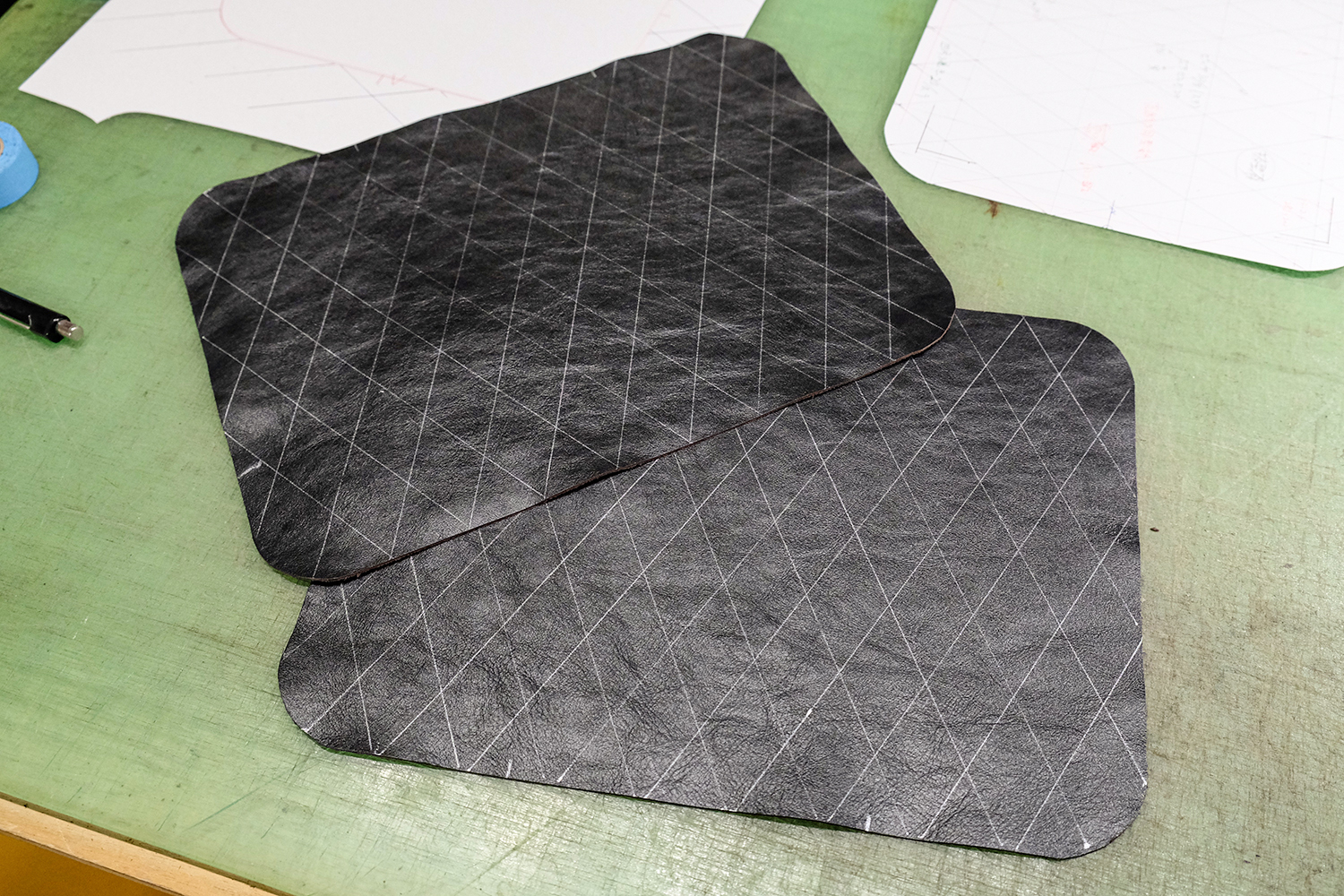
徳永氏が自作したテンプレートに馬革を置き、ダイヤキルトのガイドラインを引いていく。ダイヤキルトの大きさ、角度は従来モデルを継承している。
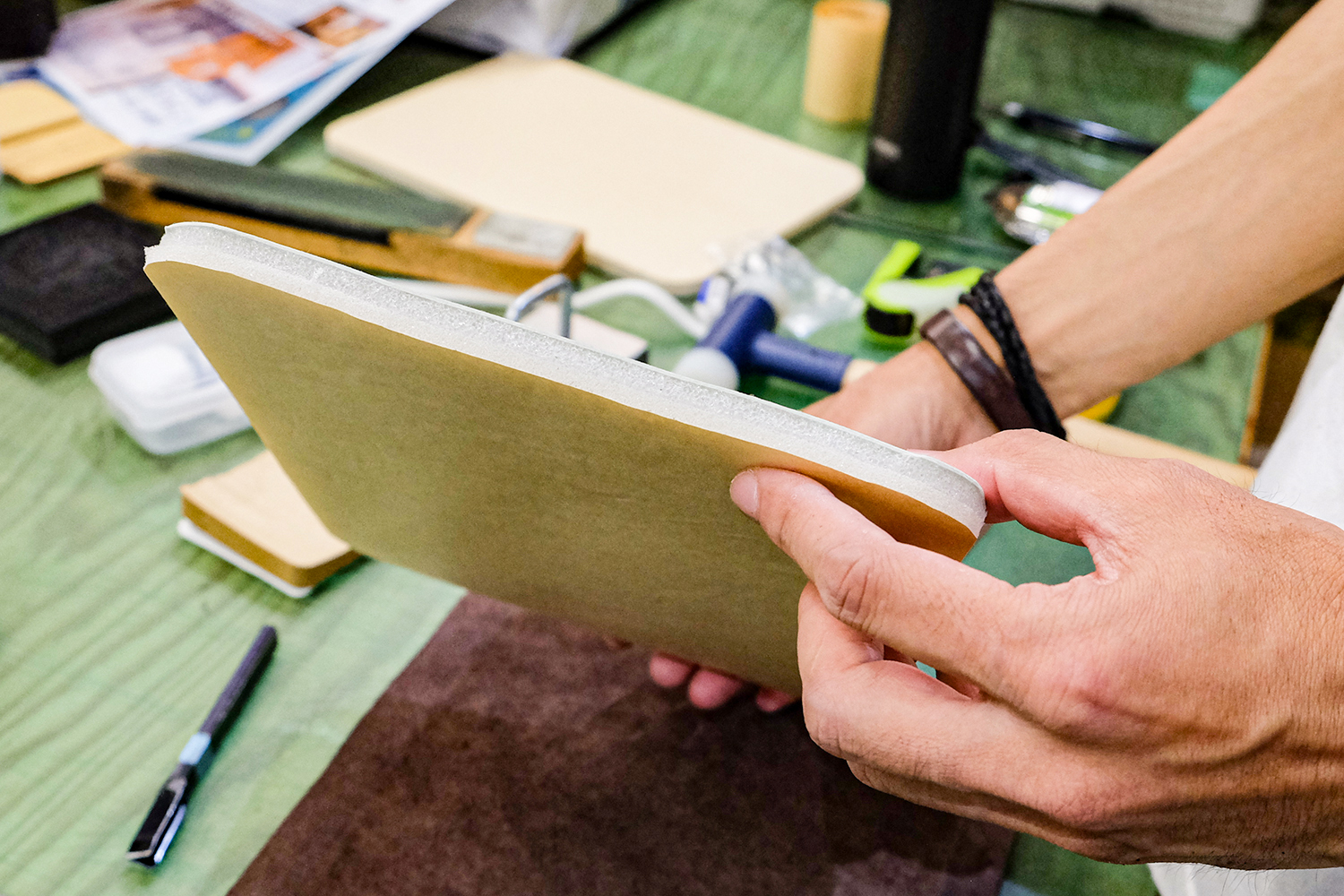
ダイヤキルト部分に挟み込む芯材。複数の種類&厚みを組み合わせ、試作を繰り返し、ようやく辿り着いた理想の固さと弾力。従来モデルよりも立体的でセクシーな盛り上がりを目指したため、厚みも増している。
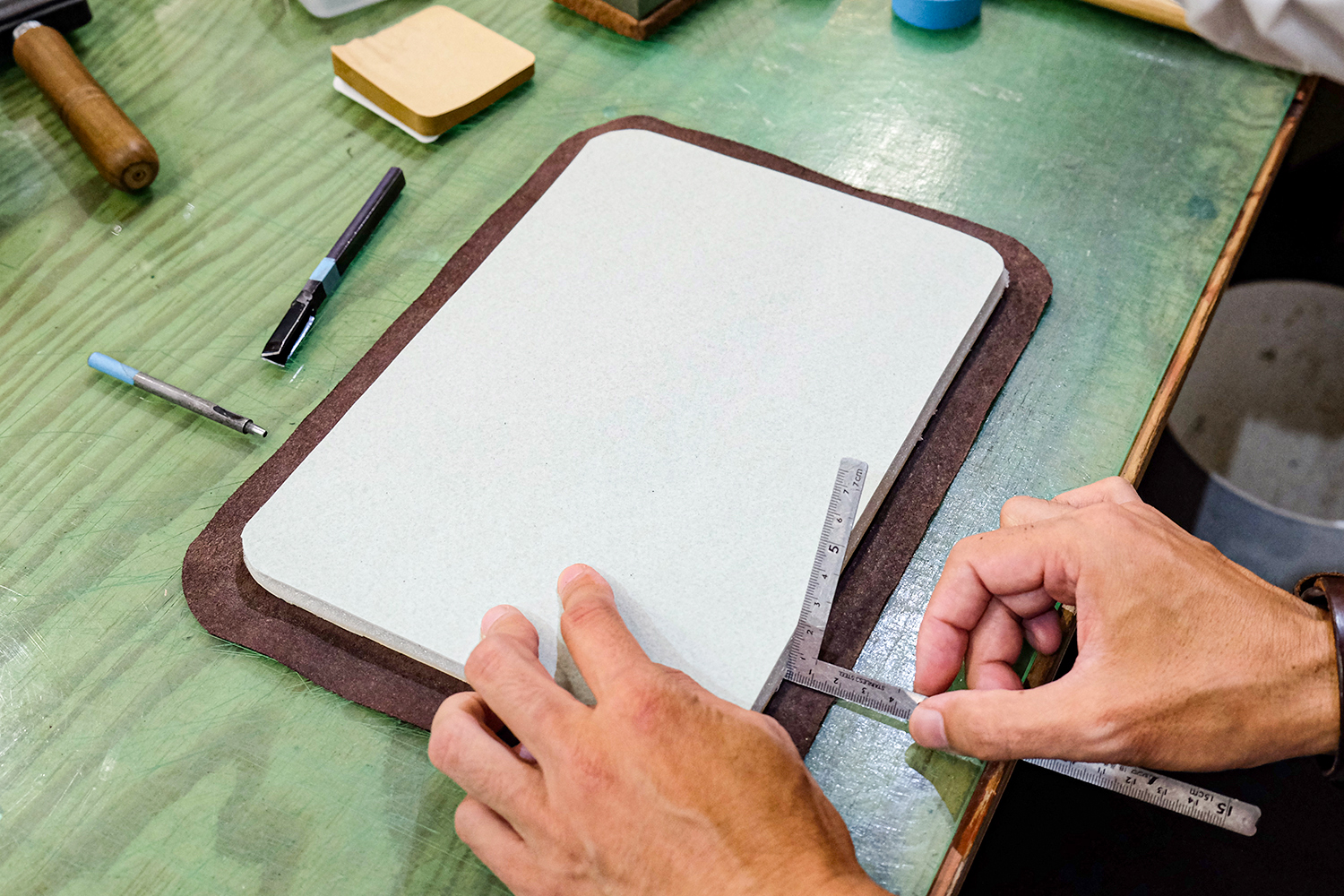
馬革に芯材を貼り合わせる。ミリ単位の緻密な作業が続く。
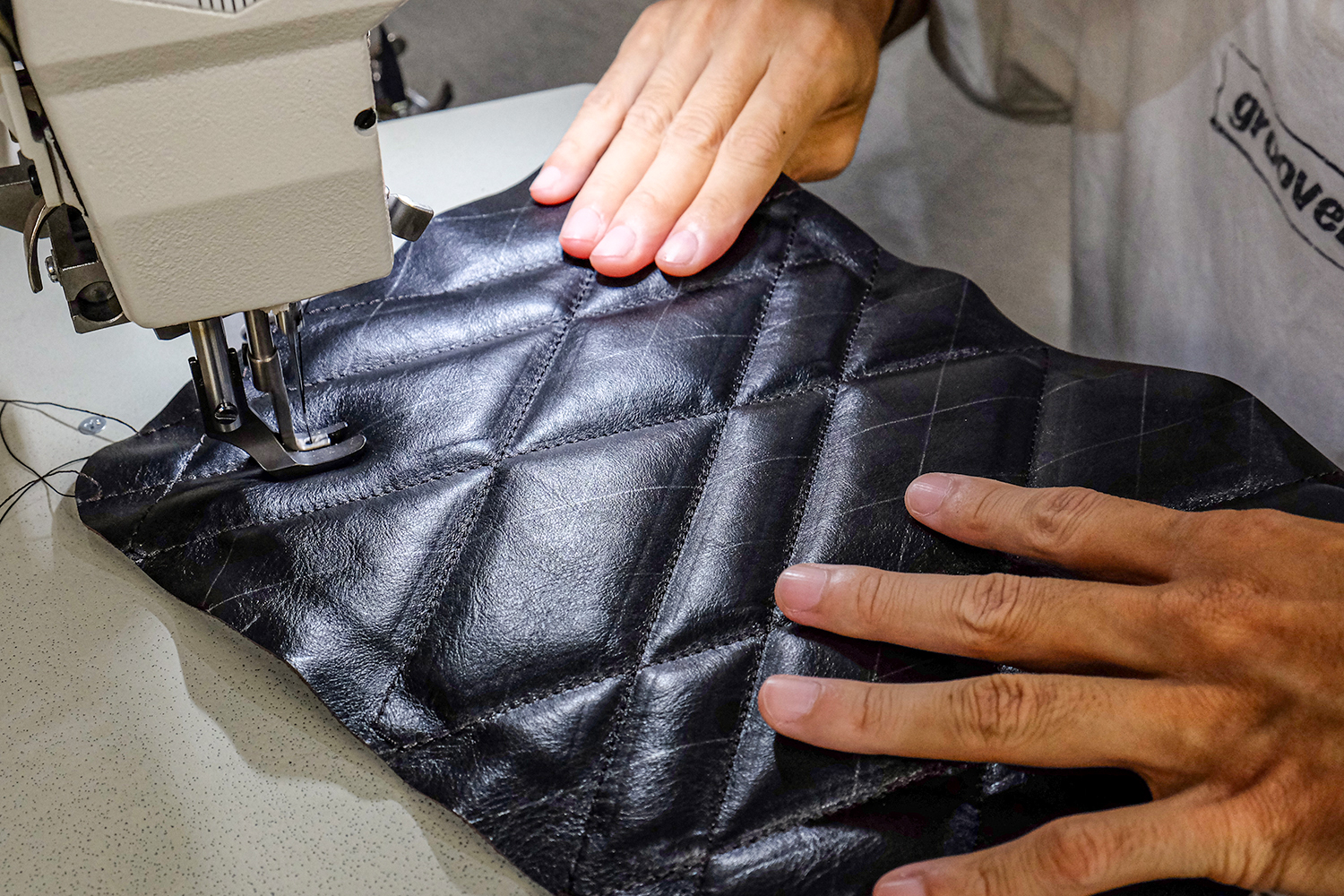

慎重にミシンを走らせ、ダイヤキルトを構築していく。無数に交差するガイドライン。決まった縫製順序があるわけではなく、革質や状態を確認しながら、盛り上がりが均等になるように縫い進める。
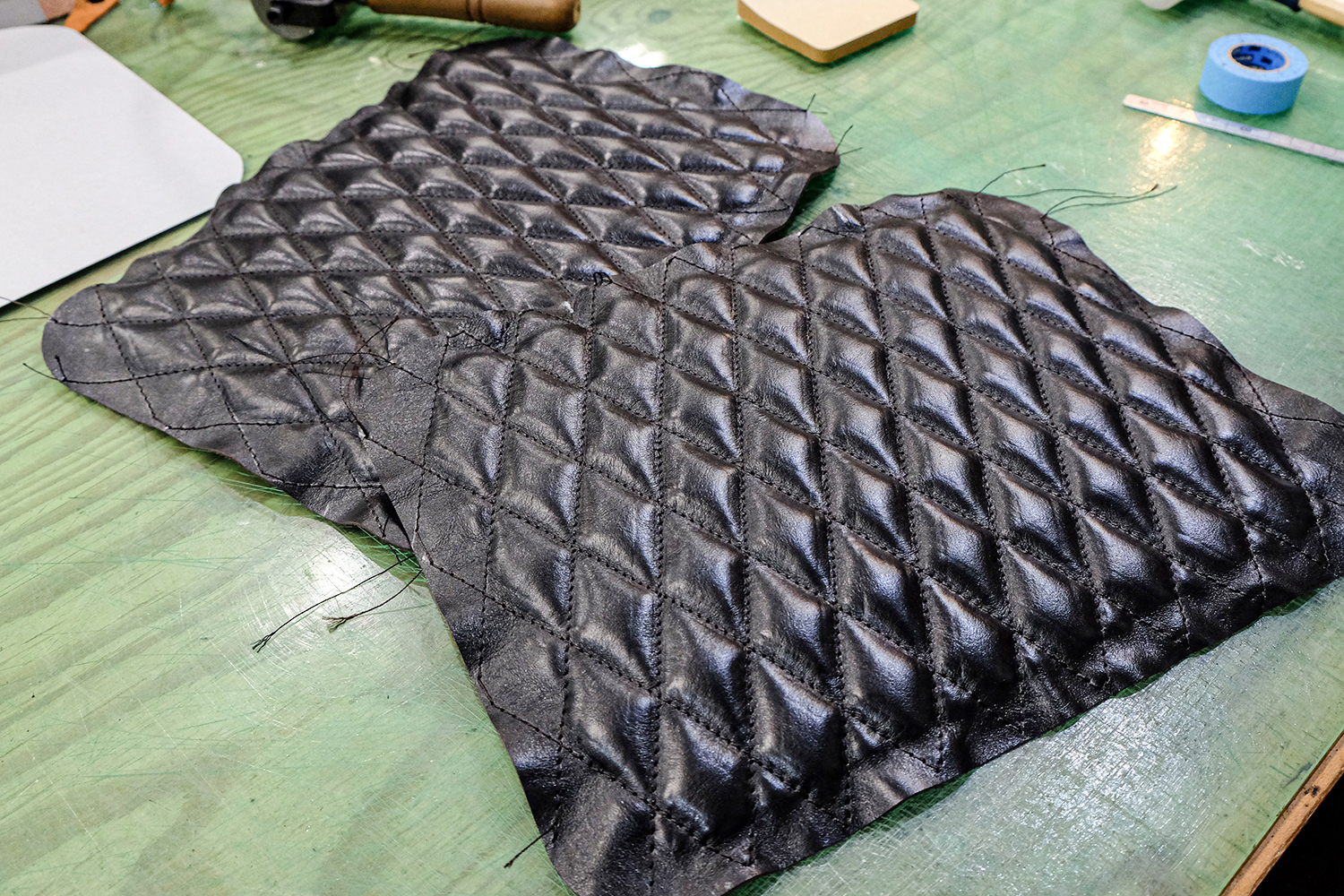
完成したダイヤキルト。新たな「OG-6」では縫製糸を太くすることで、ダイヤキルトを一層際立たせている。ブリブリ過ぎて下品にならず、アダルトでセクシーな程良い立体感。手触りも抜群。
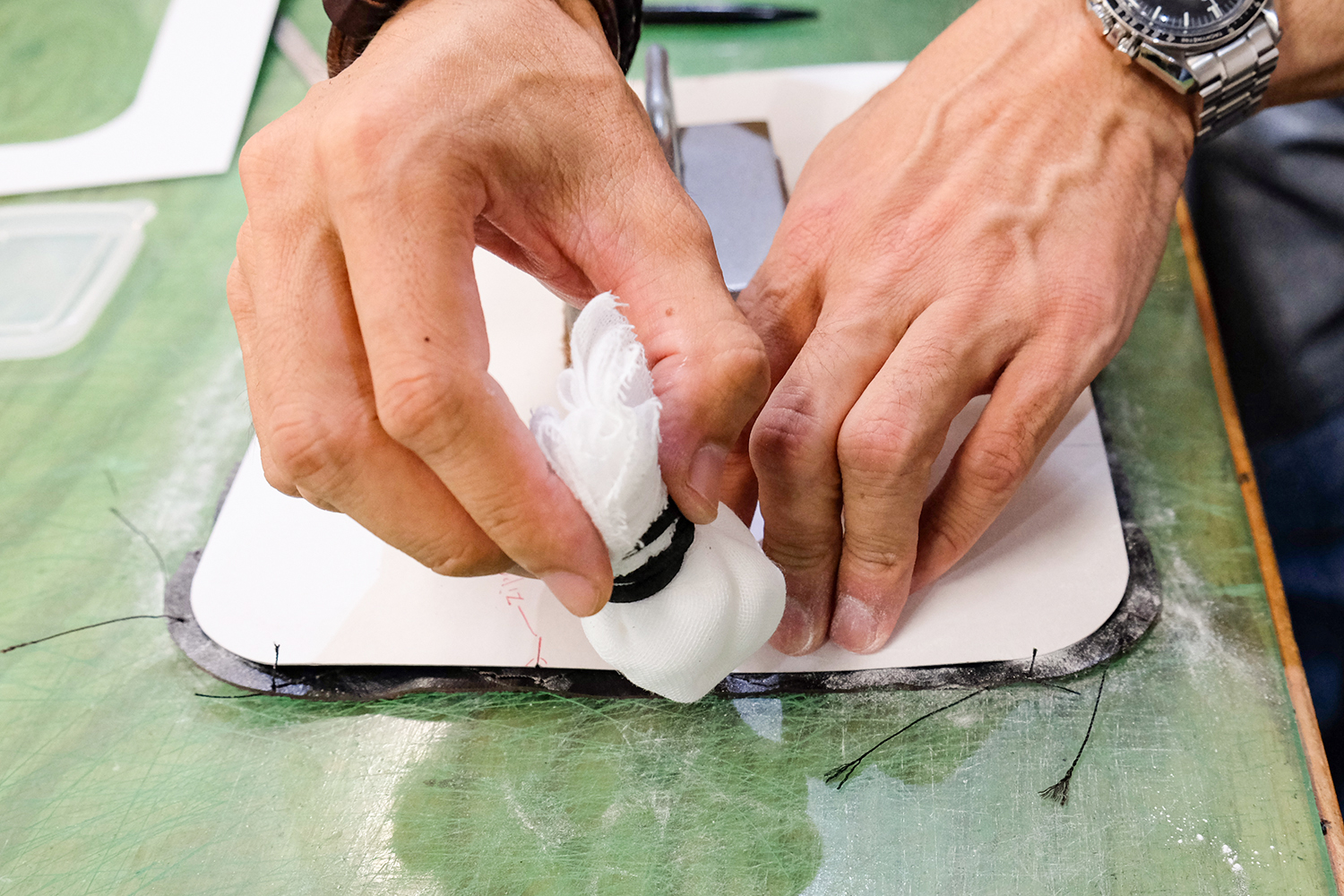
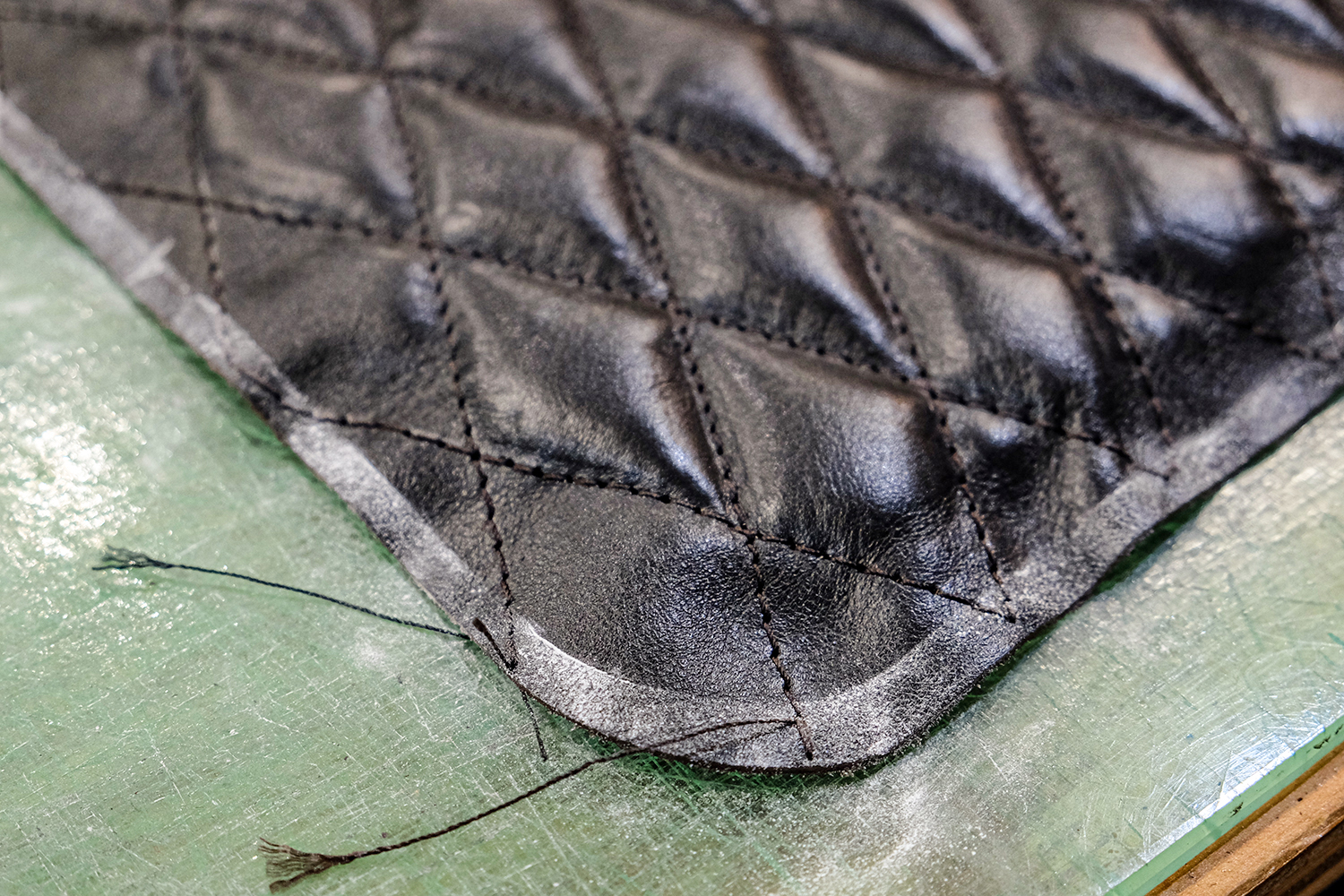
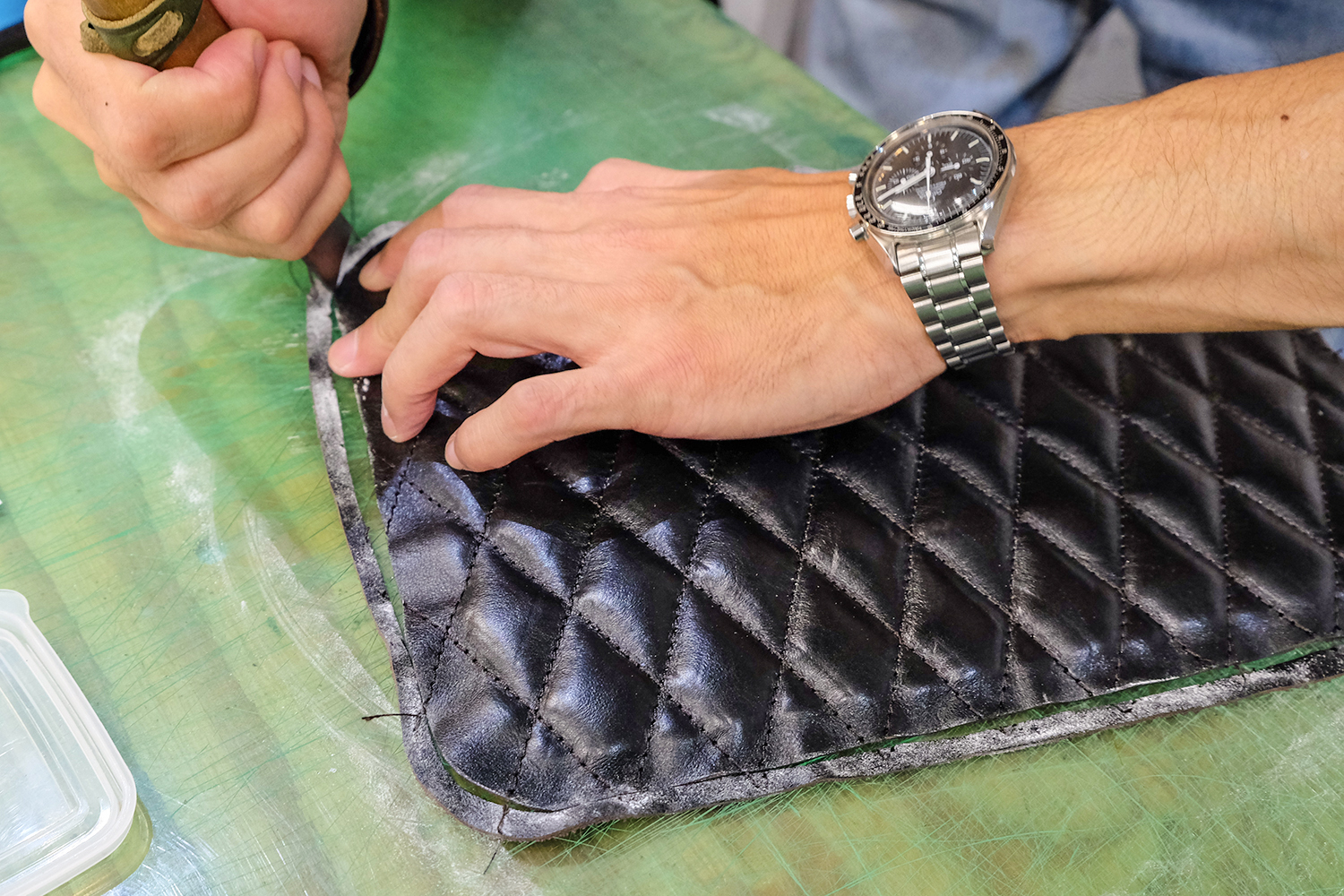
立体的なダイヤキルトは縫い縮みや歪みが発生することがあるため、実寸よりも若干大きめに作っている。縫製完了後、型紙を置いてパウダーを含ませた布で叩き、余分な部分をマーキング。丁寧にハンドカットする。
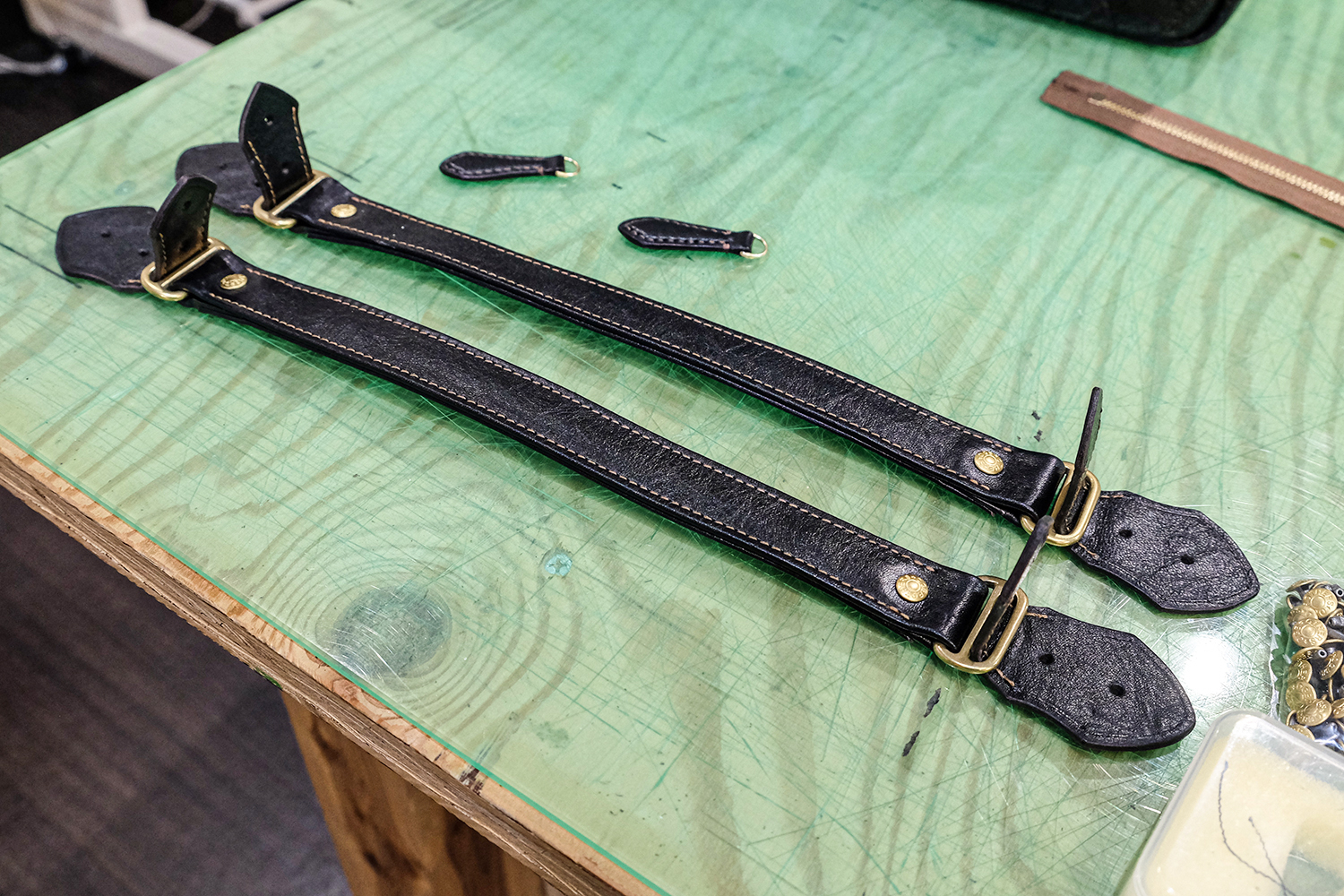
ハンドルの長さ&太さも従来モデルと同寸。根革とハンドルを繋ぐ金具も、従来モデルとまったく同じものを用意した。
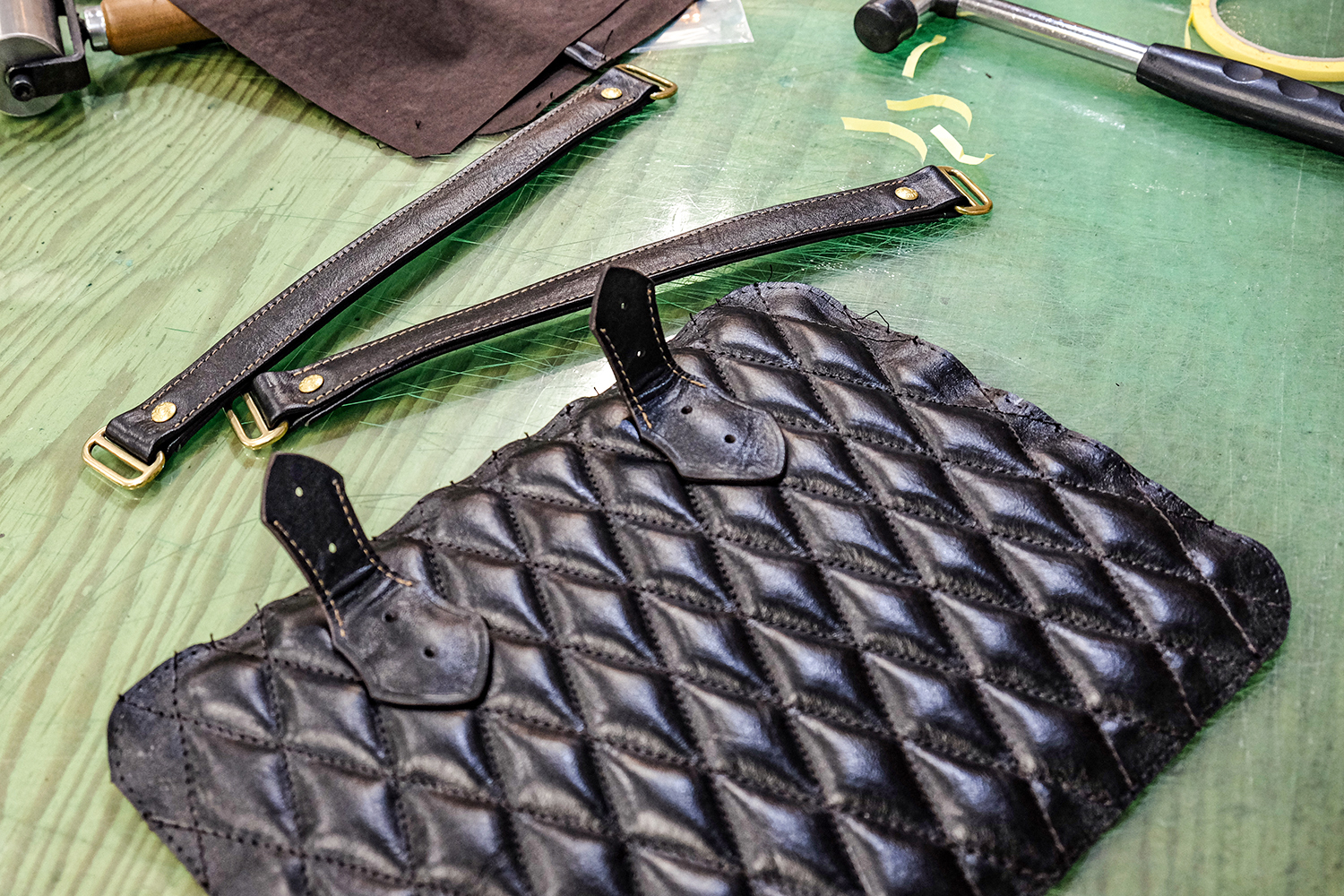
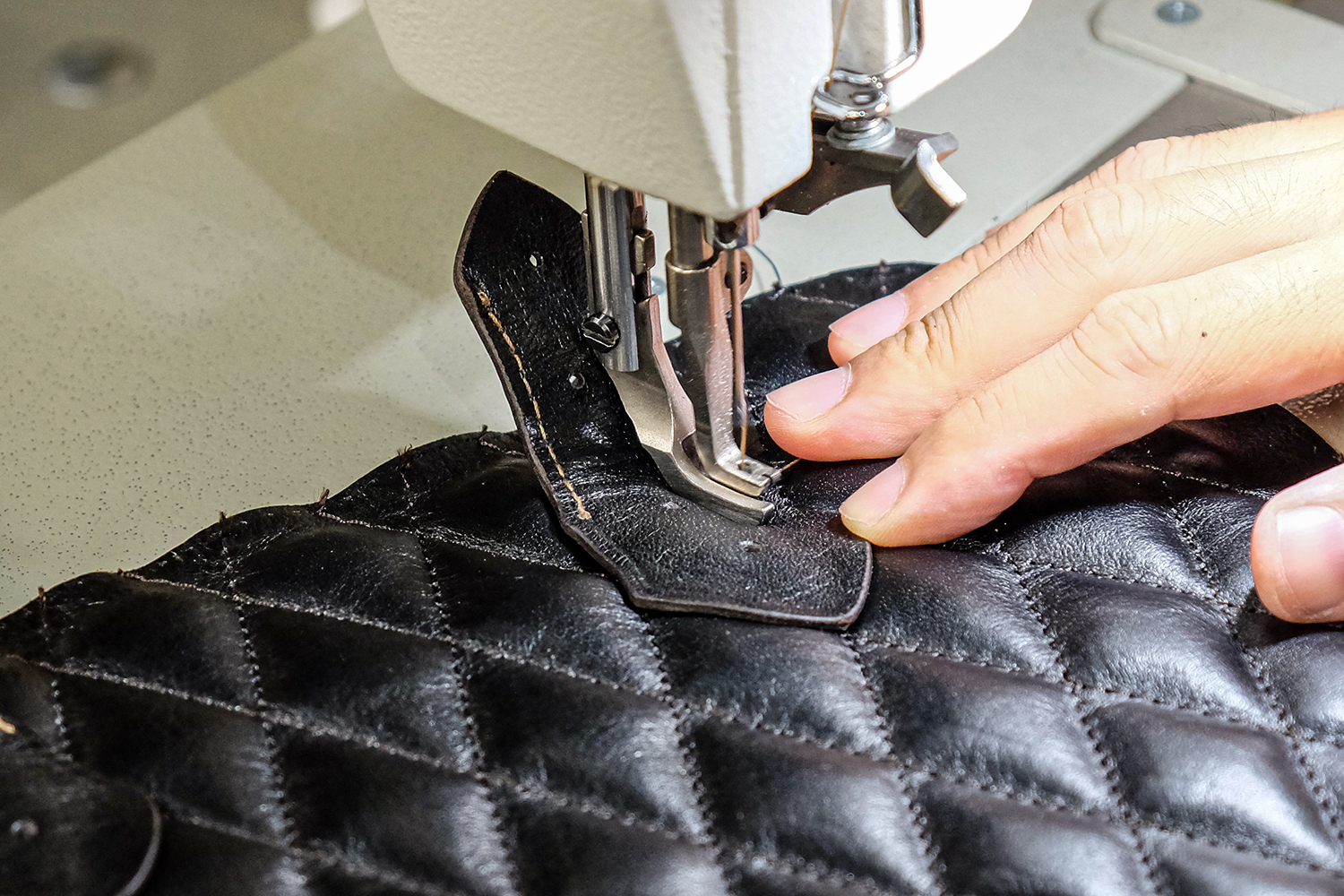
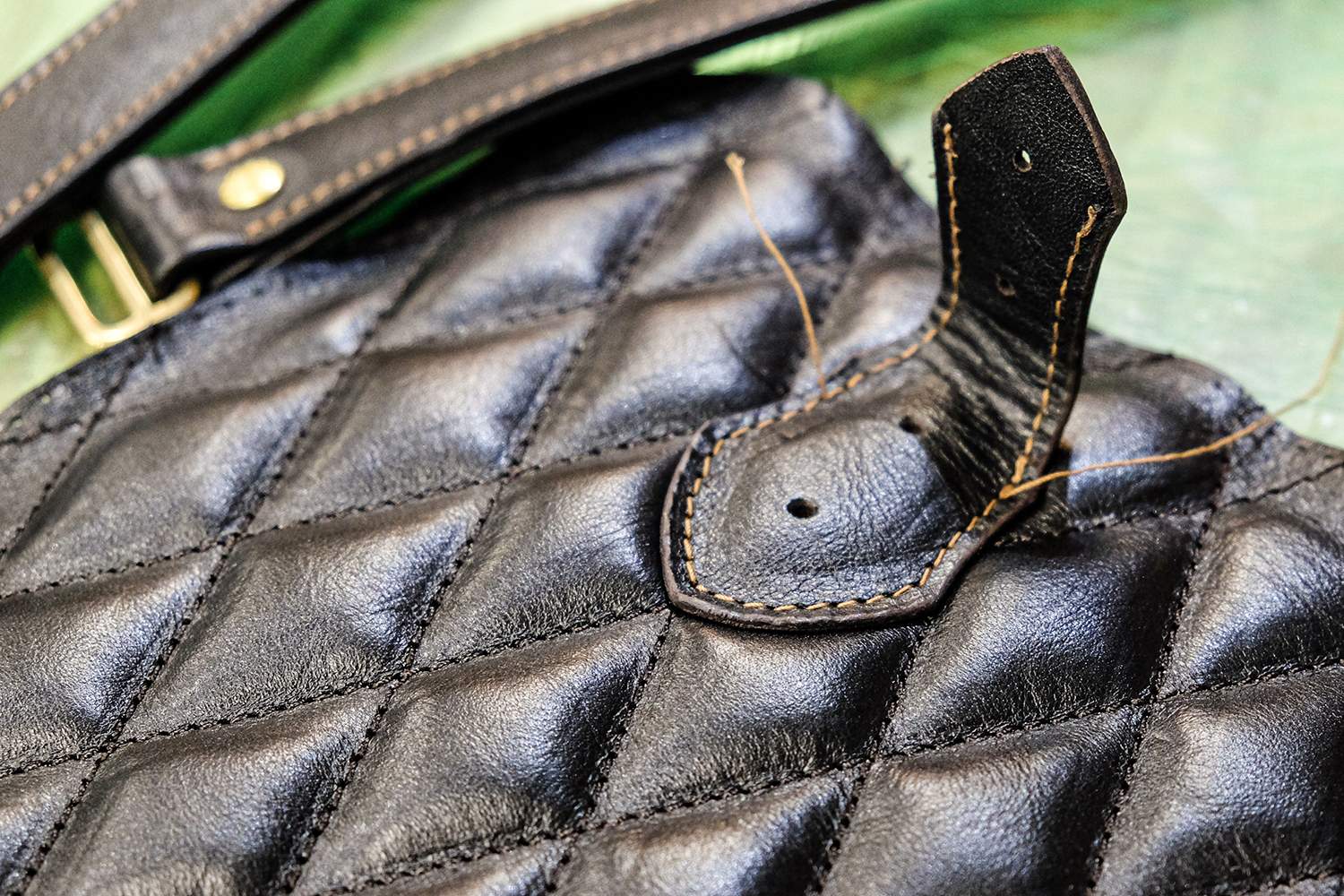
根革をボディに両面テープで貼り付けて位置決めする。その後、ミシンをゆっくりと走らせて縫い付ける。従来モデルよりもダイヤキルトの膨らみがあるので、簡単そうに見えて難しい。縫い付けた根革の中央部分が下地のダイヤキルトによって盛り上がっている。
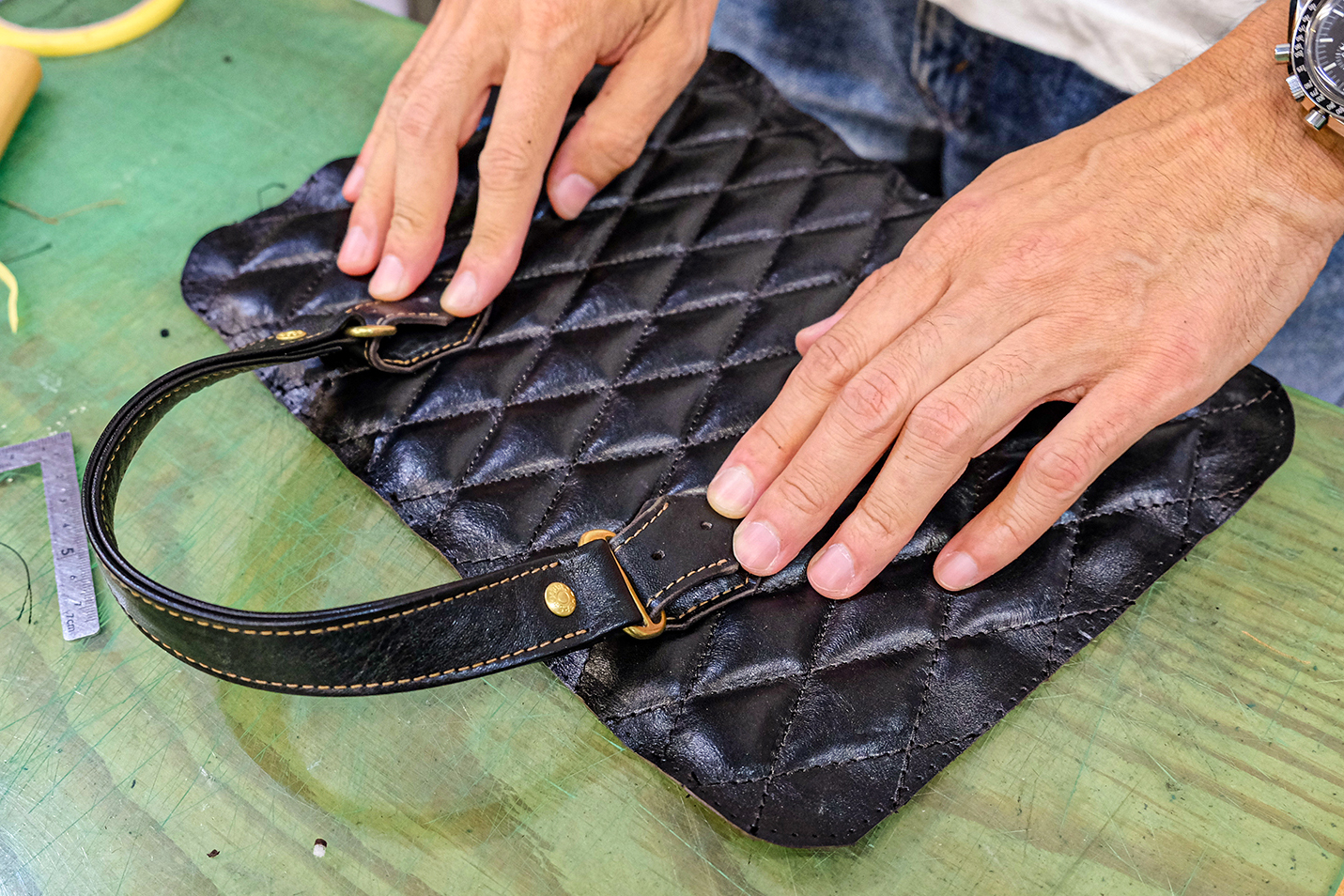
金具を介してハンドルを取り付け、縫い合わせの位置を再確認。
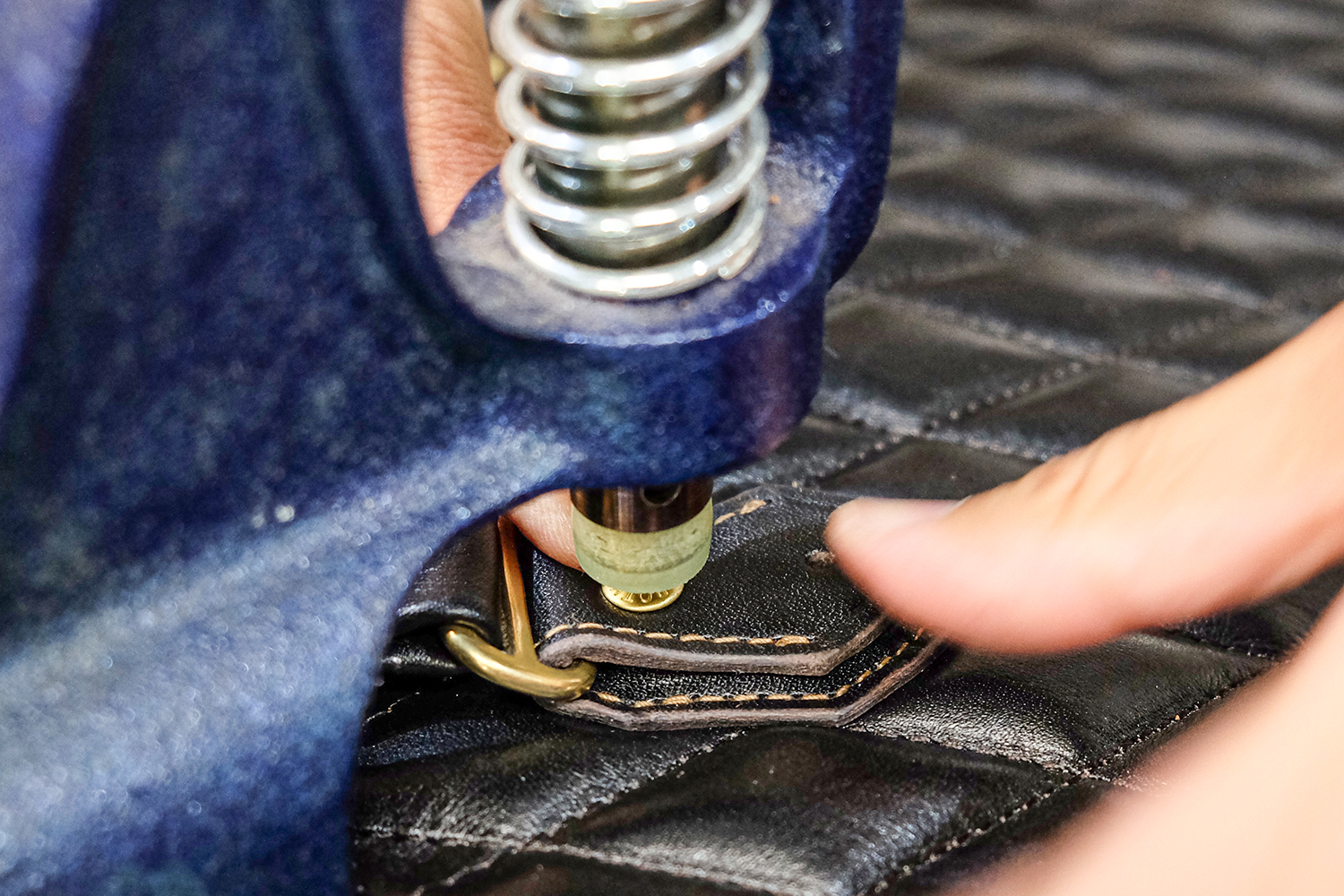

折り返した根革を曲がって縫い付けてしまわないように、2個のカシメのうち1個を先に打ち込んで根革を固定。
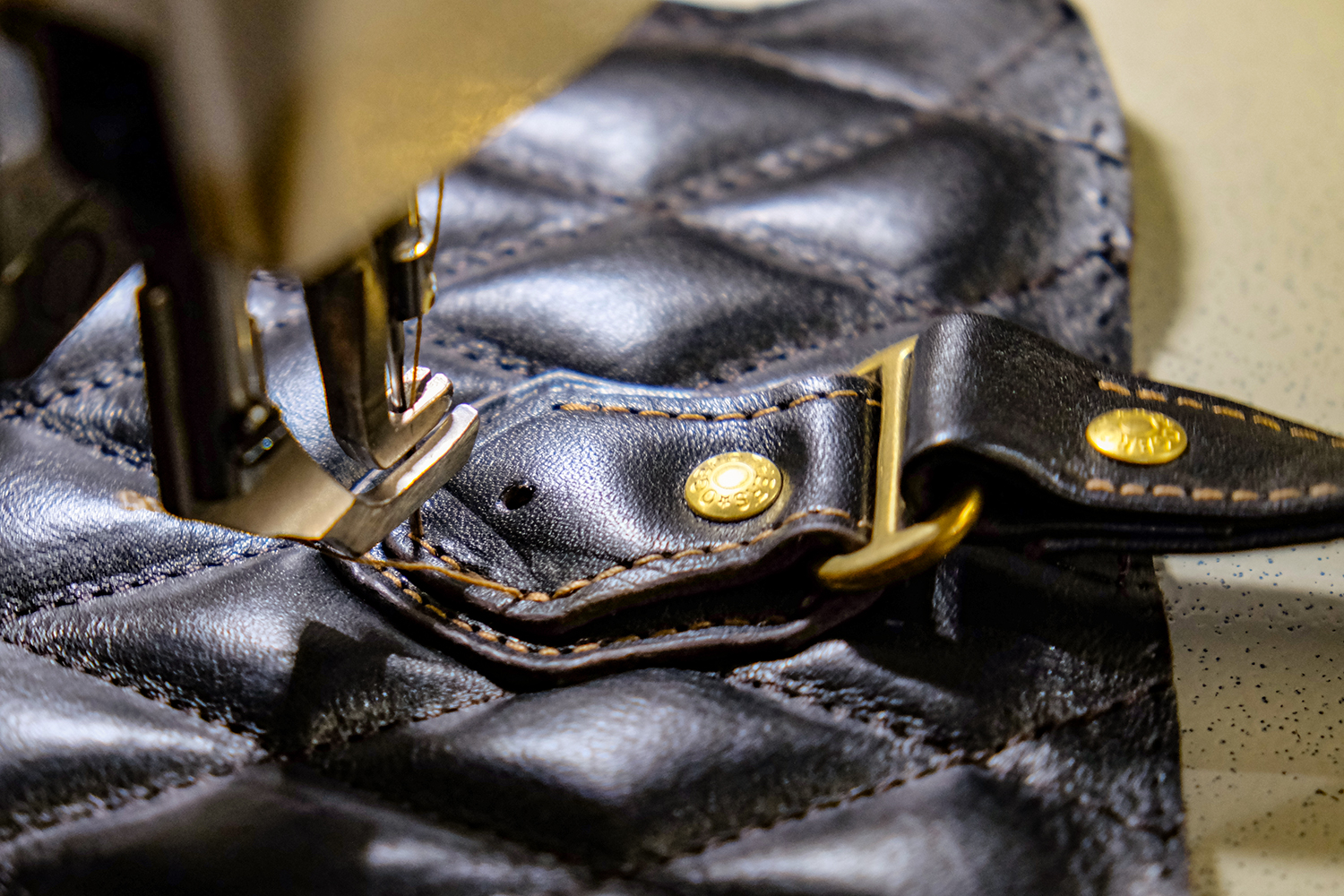
その後、根革の折り返し部分を縫い付ける。凹凸があり、縫う箇所も短いので慎重な作業が求められる。
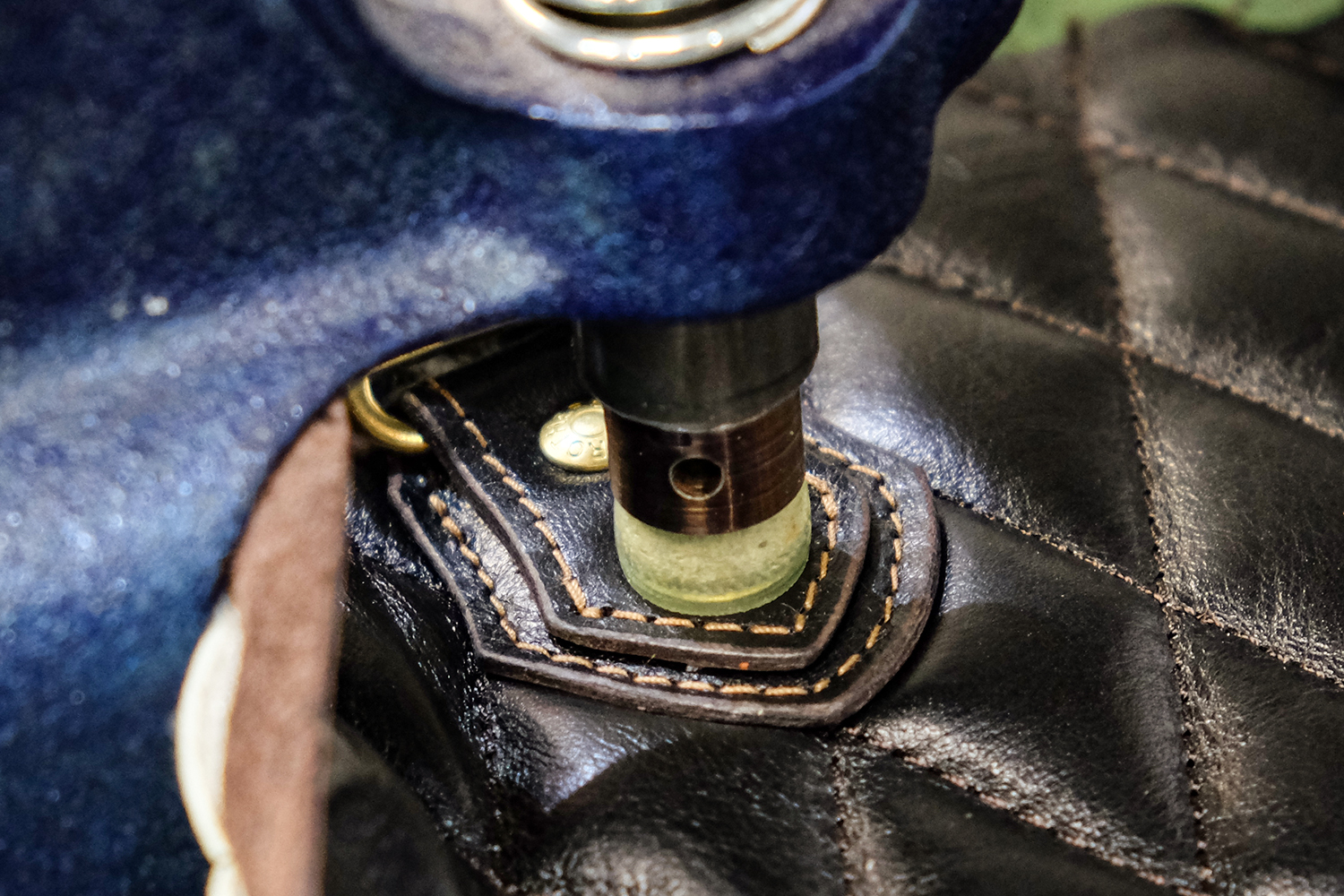
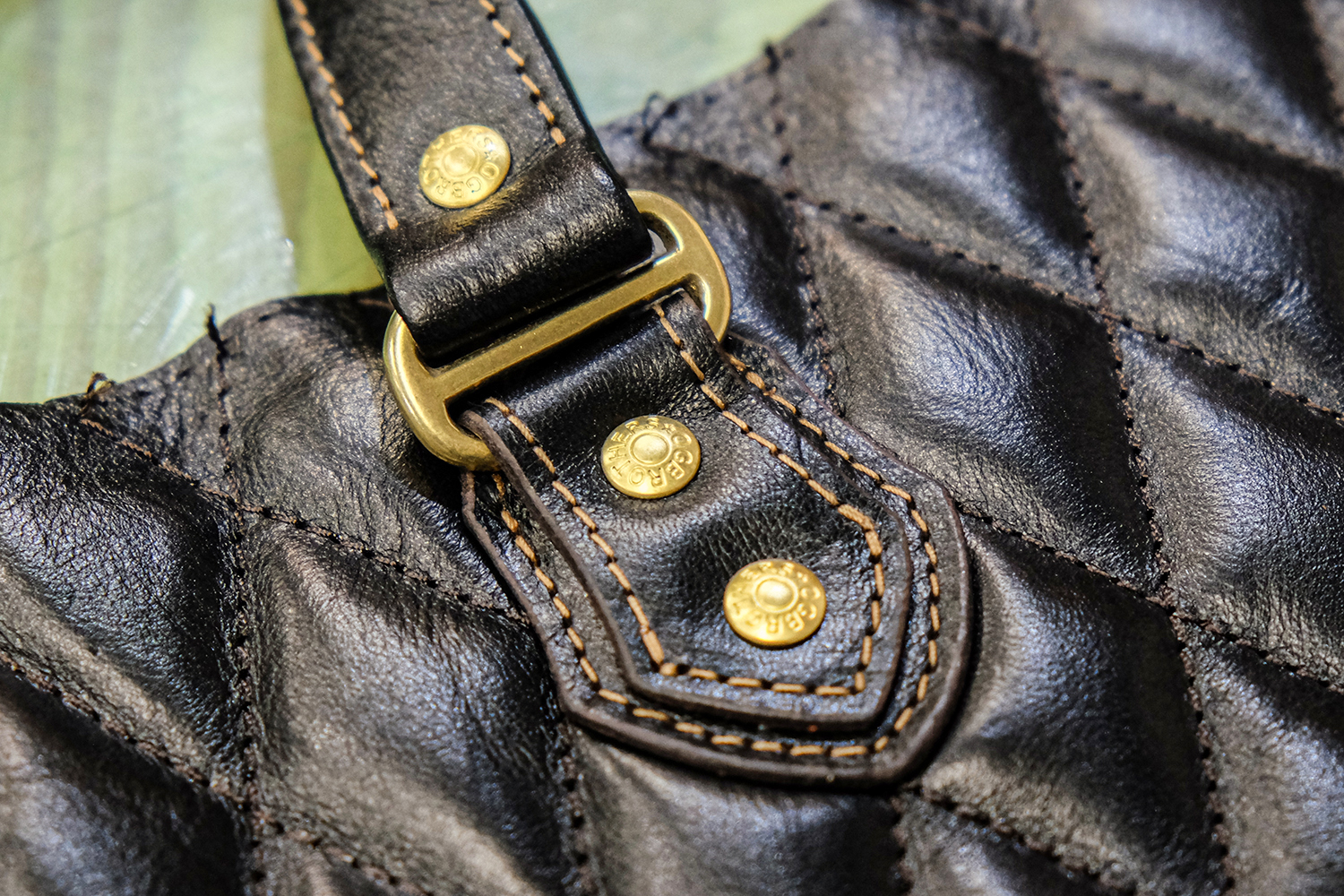
最後に2つ目のカシメを打ち込んで完了。効率は下がるが、より美しい仕上がりを追求する徳永氏の独自の作業手順に、職人魂を垣間見ることができた。
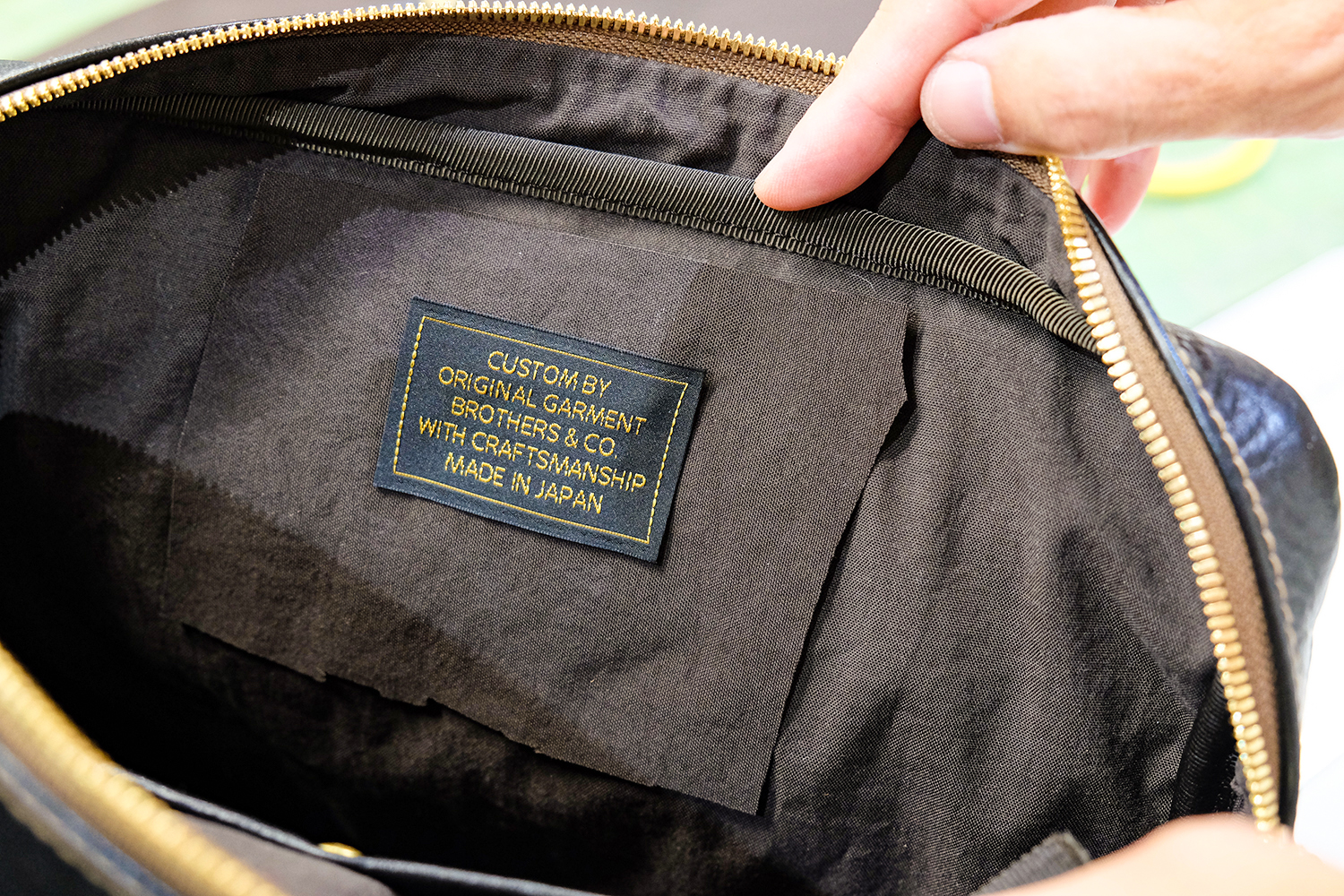
従来モデルはフラットヘッドとオージーブロスのラベルが並んでいたが、今モデルからはオージーブロスのラベルのみとなる。従来モデルを使って、慎重に位置を決める。
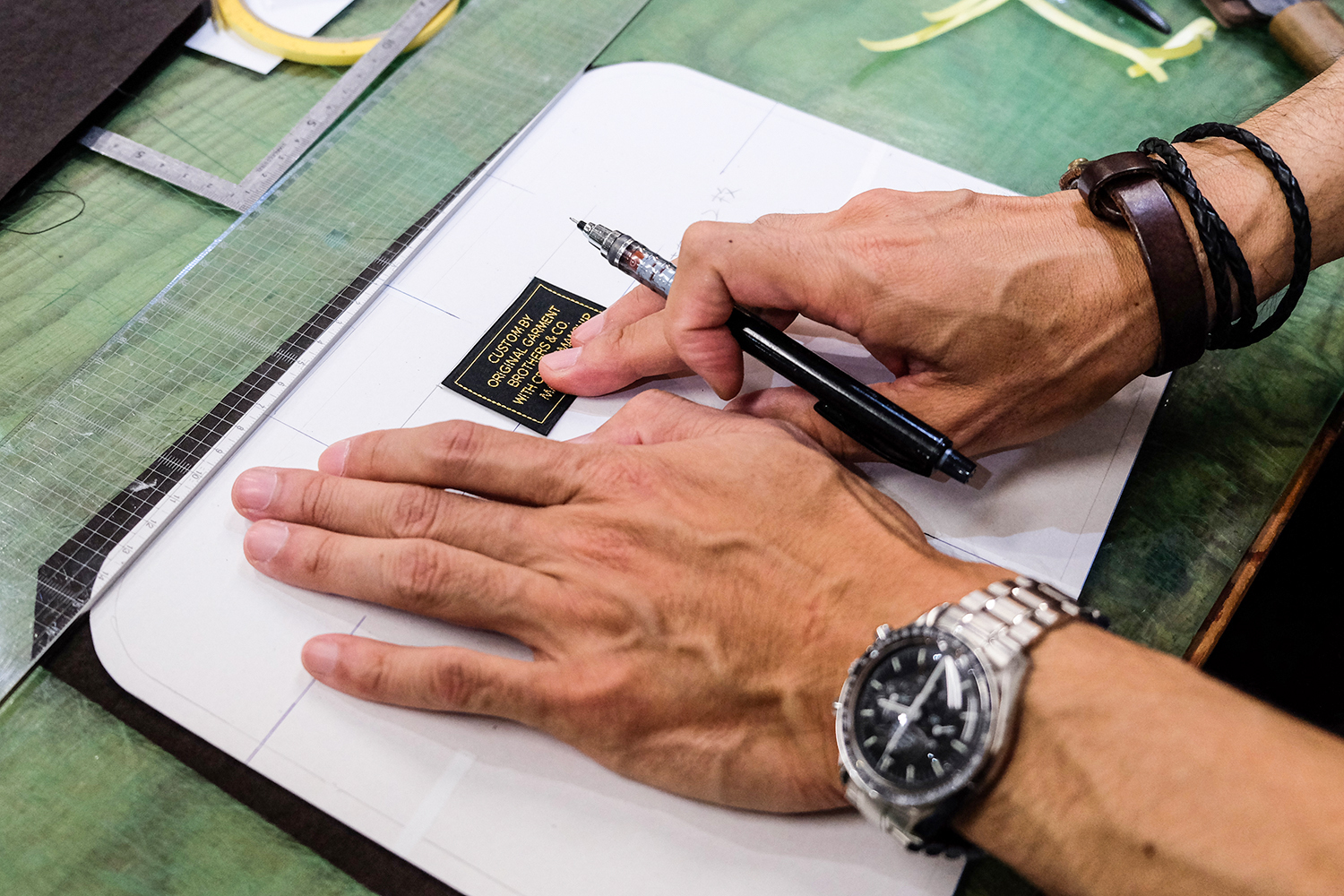
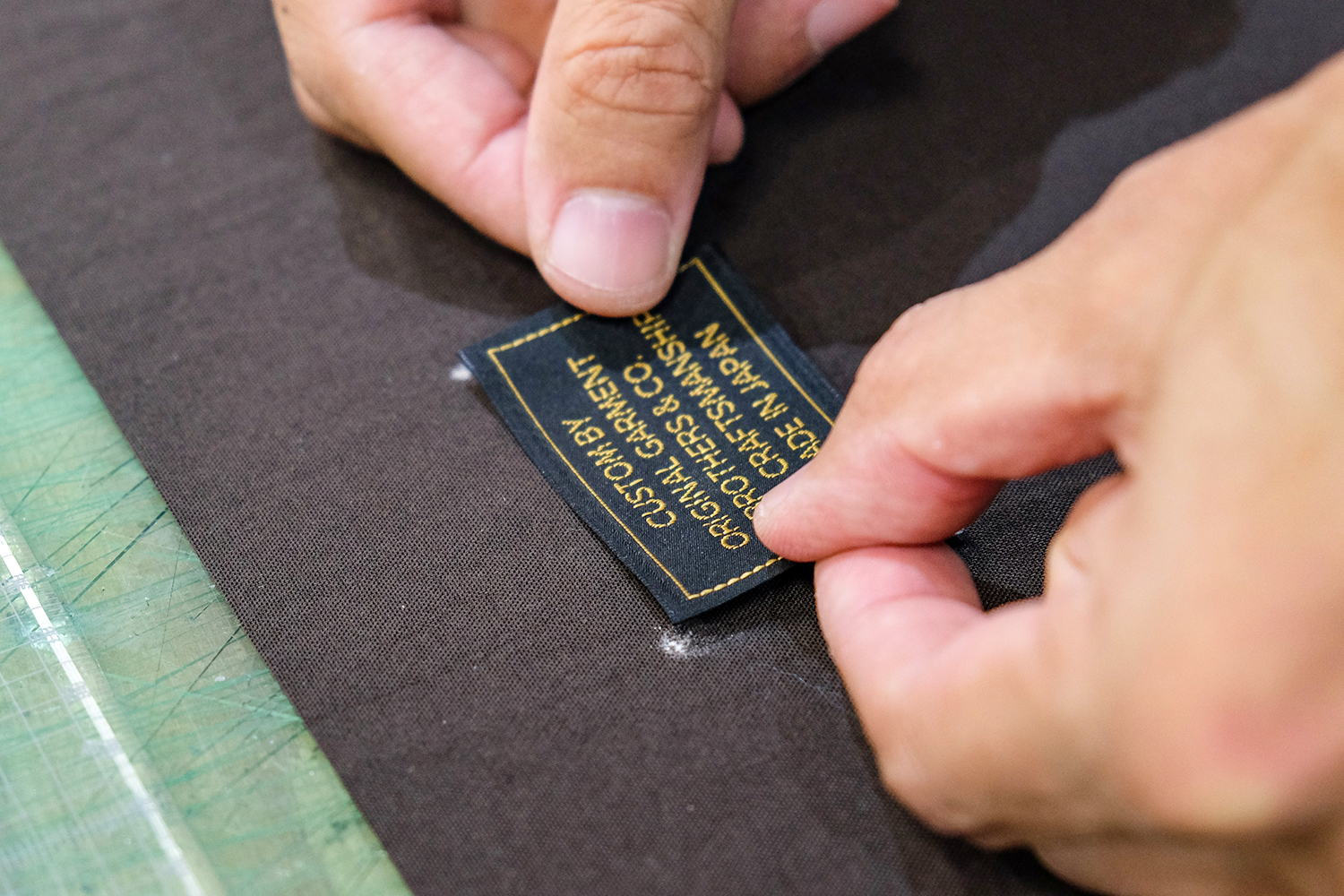
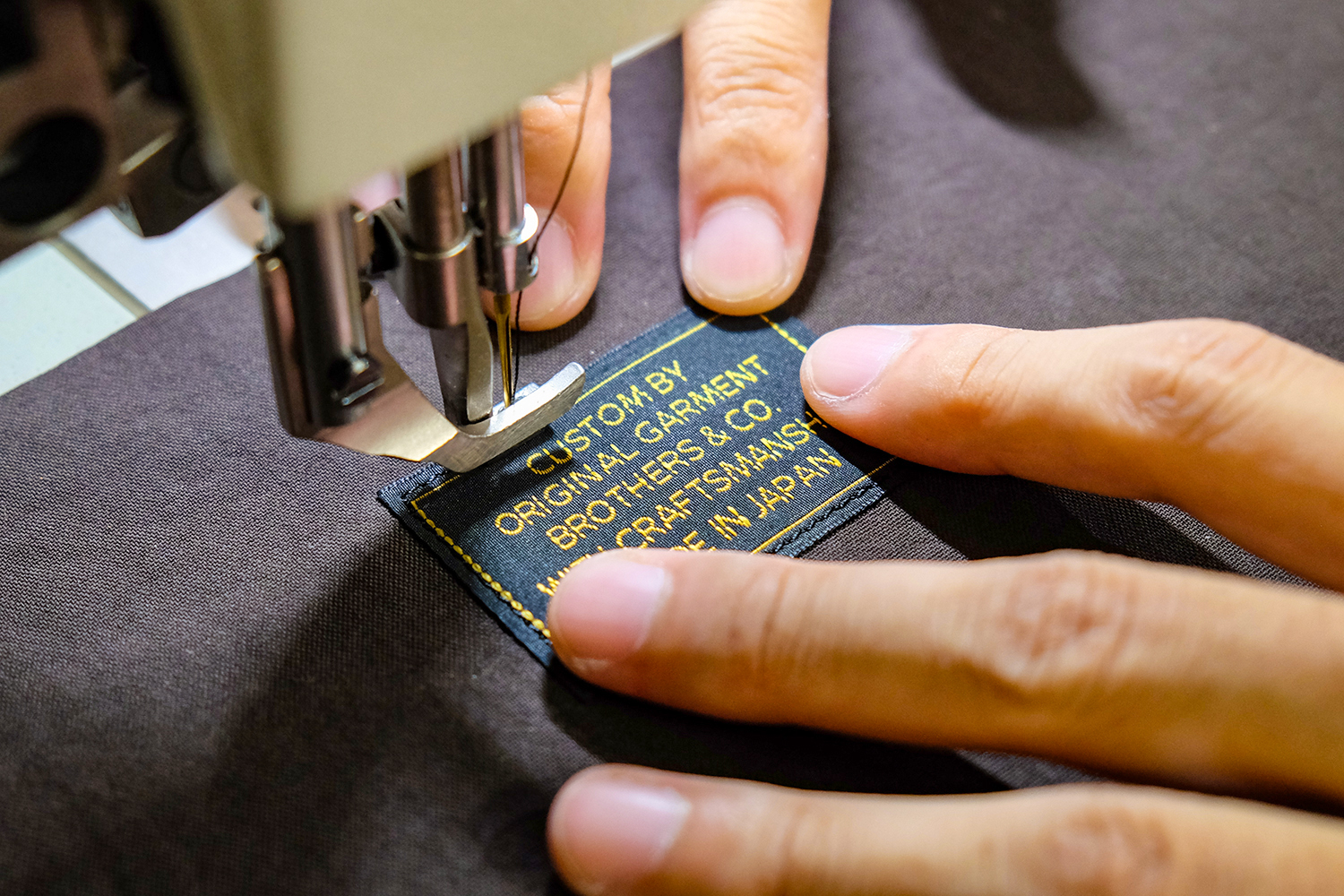
場所を決めたらテンプレートに記載し、上左右の角に穴を開ける。裏地にテンプレートを被せ、穴からパウダーでマーキング。傾かないようにオリジナルラベルを縫い付ける。
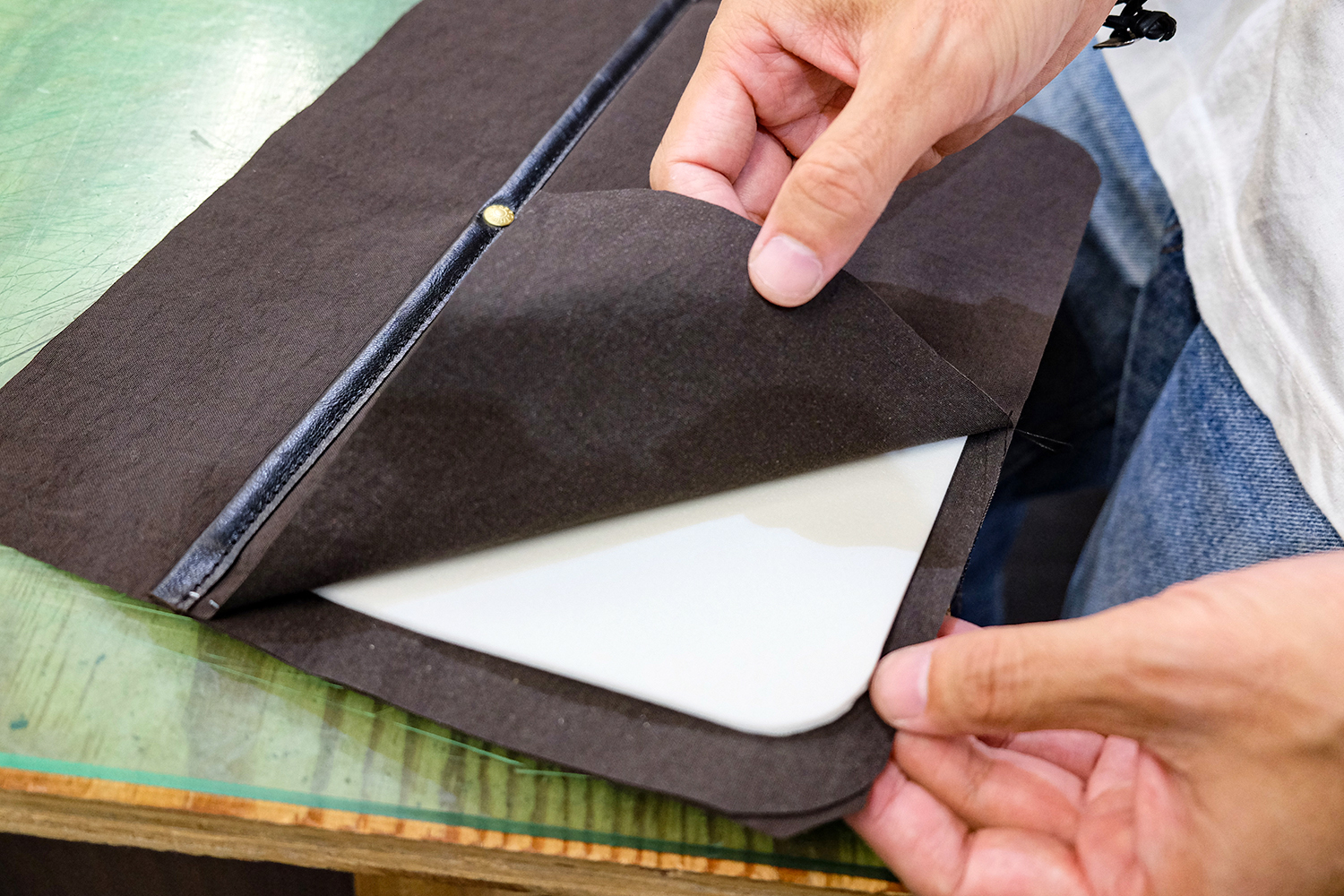
バッグ内部の片サイドには内ポケットを用意。内ポケットの仕切りに挟み込む芯材は、従来モデルよりも厚くすることにした。
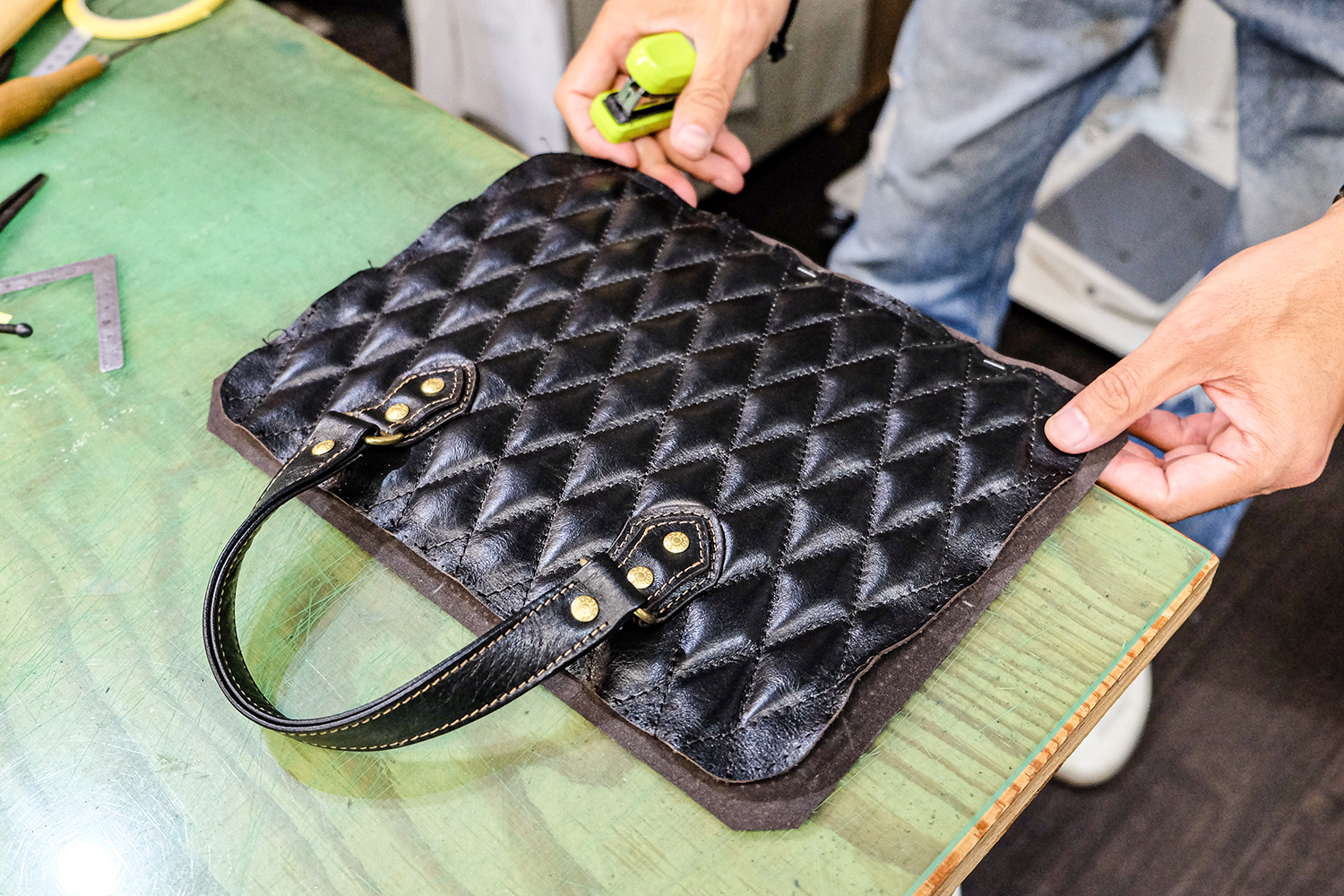
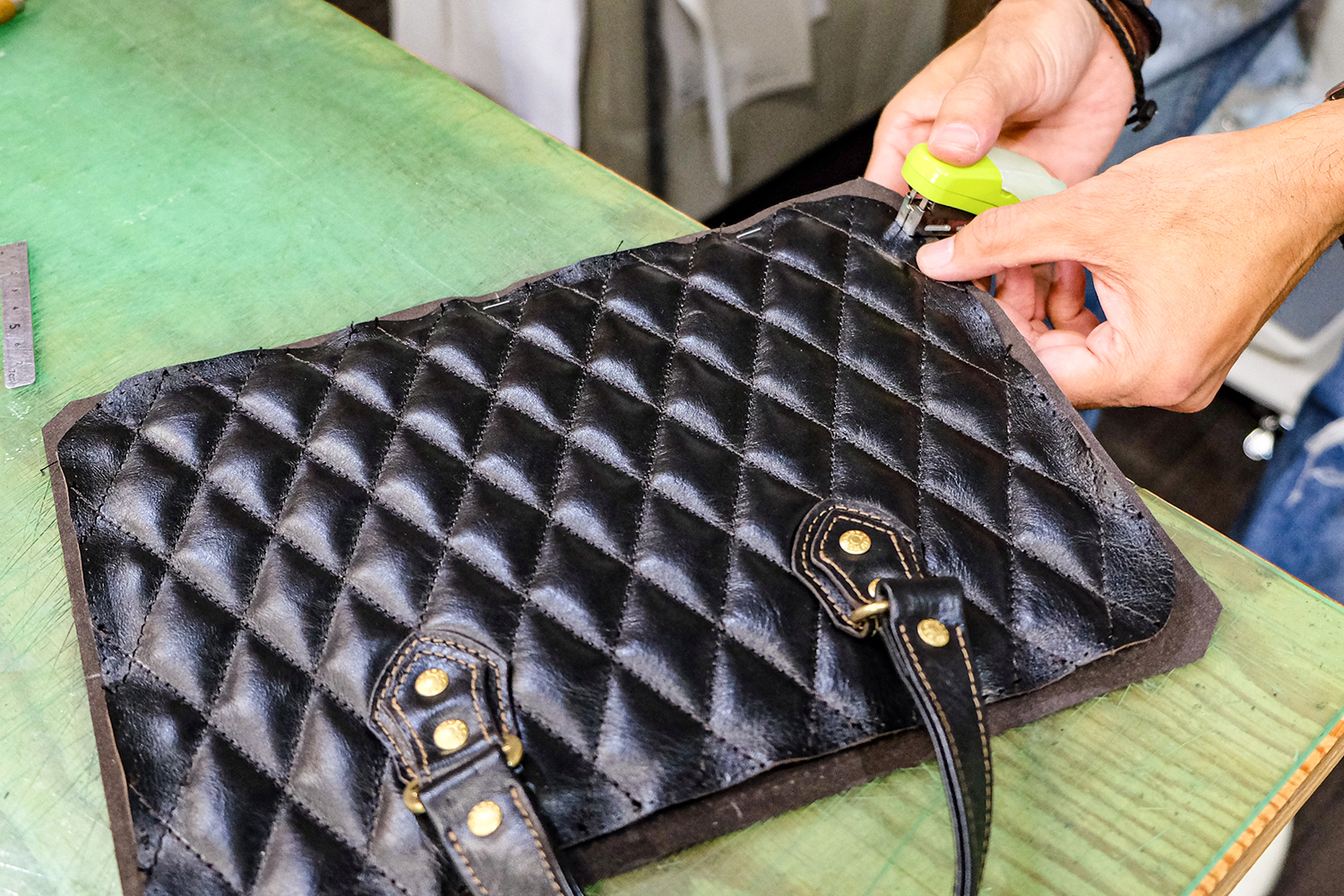
ハンドルを取り付けたボディパネルと裏地をホチキスで仮止めする。

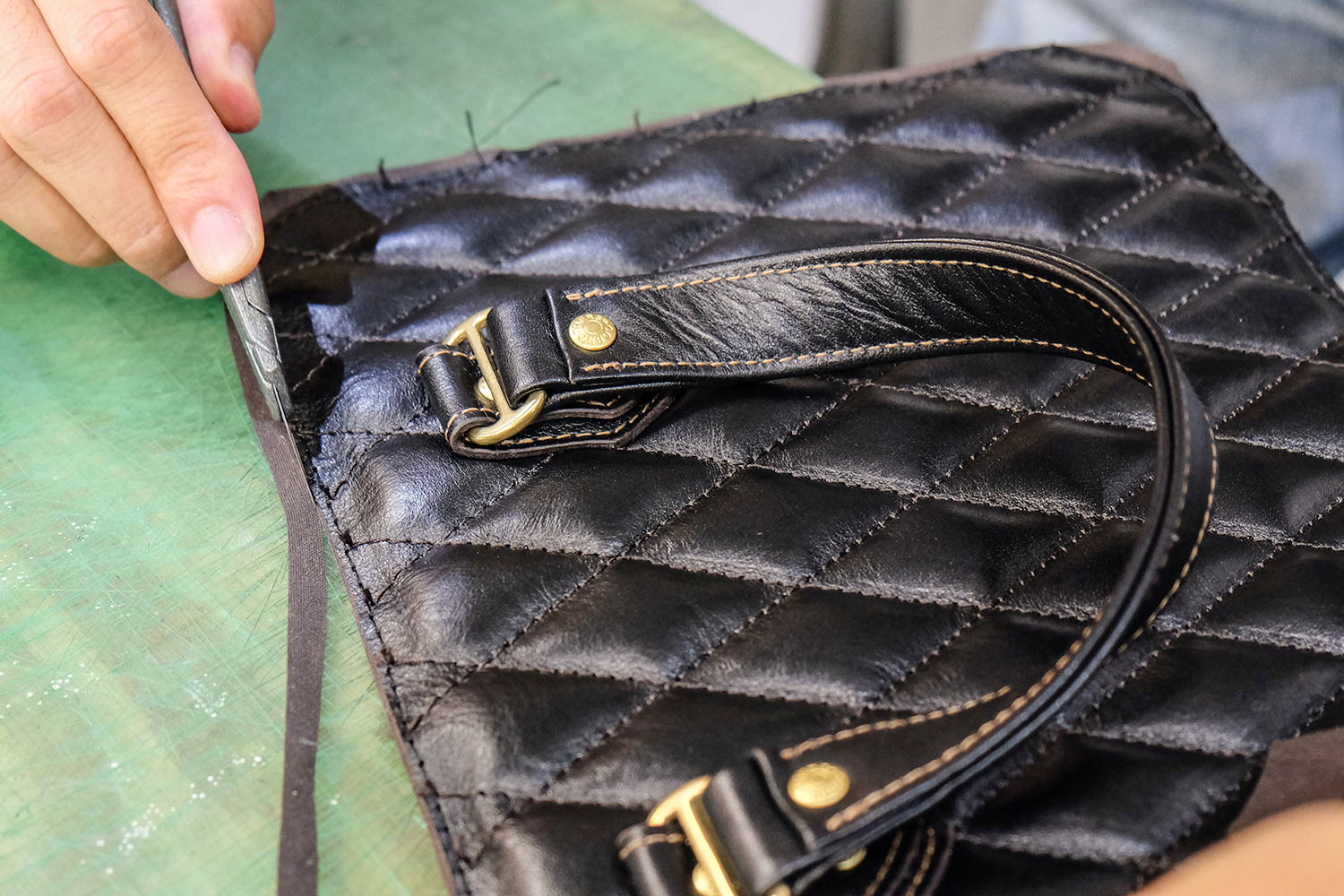
ボディパネルと裏地をミシンで縫い合わせた後、余った裏地を丁寧にカットする。
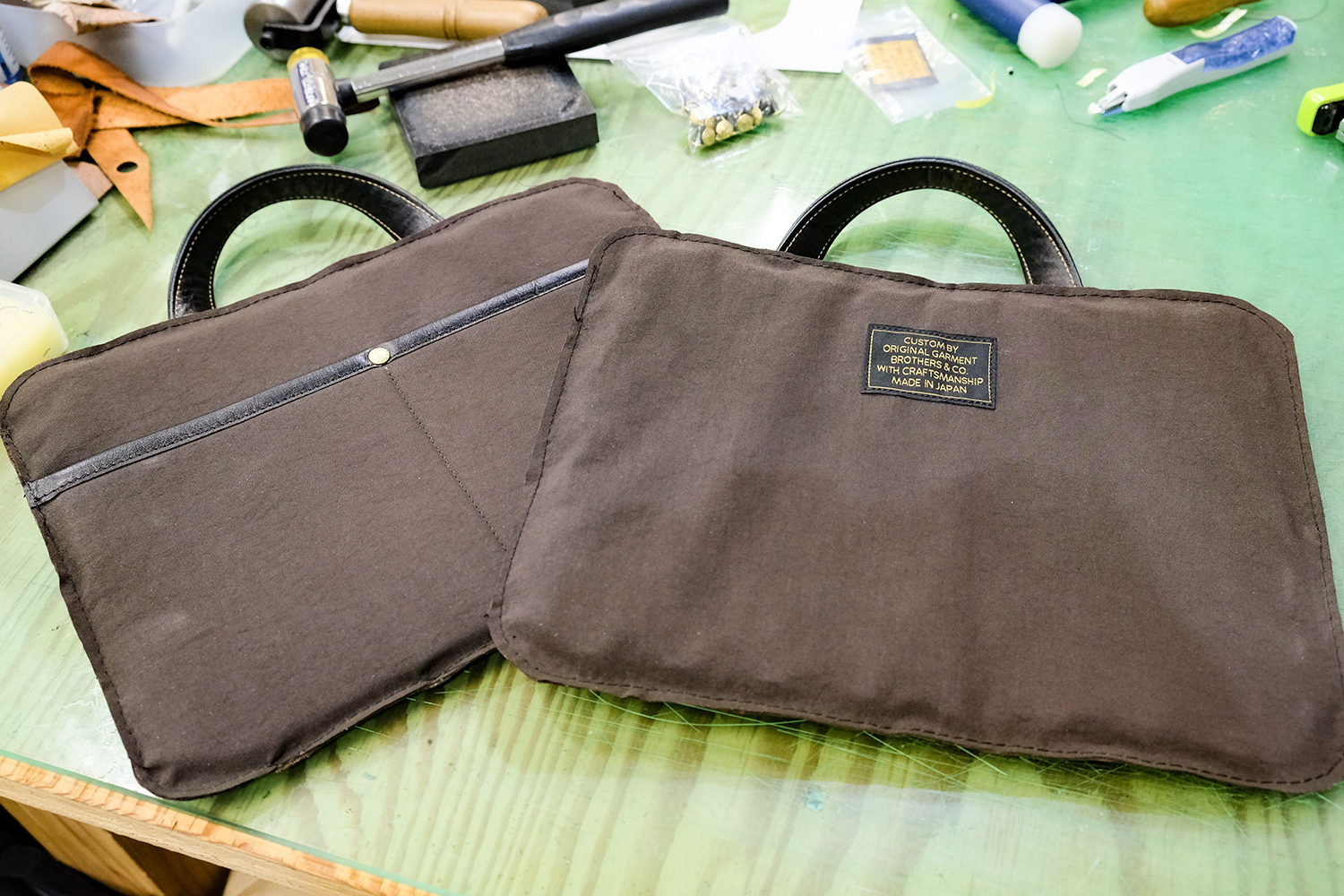
裏地が縫い付けられたボディパネル。この板状の状態を手にしただけでも、カッチリ感が体感できる。
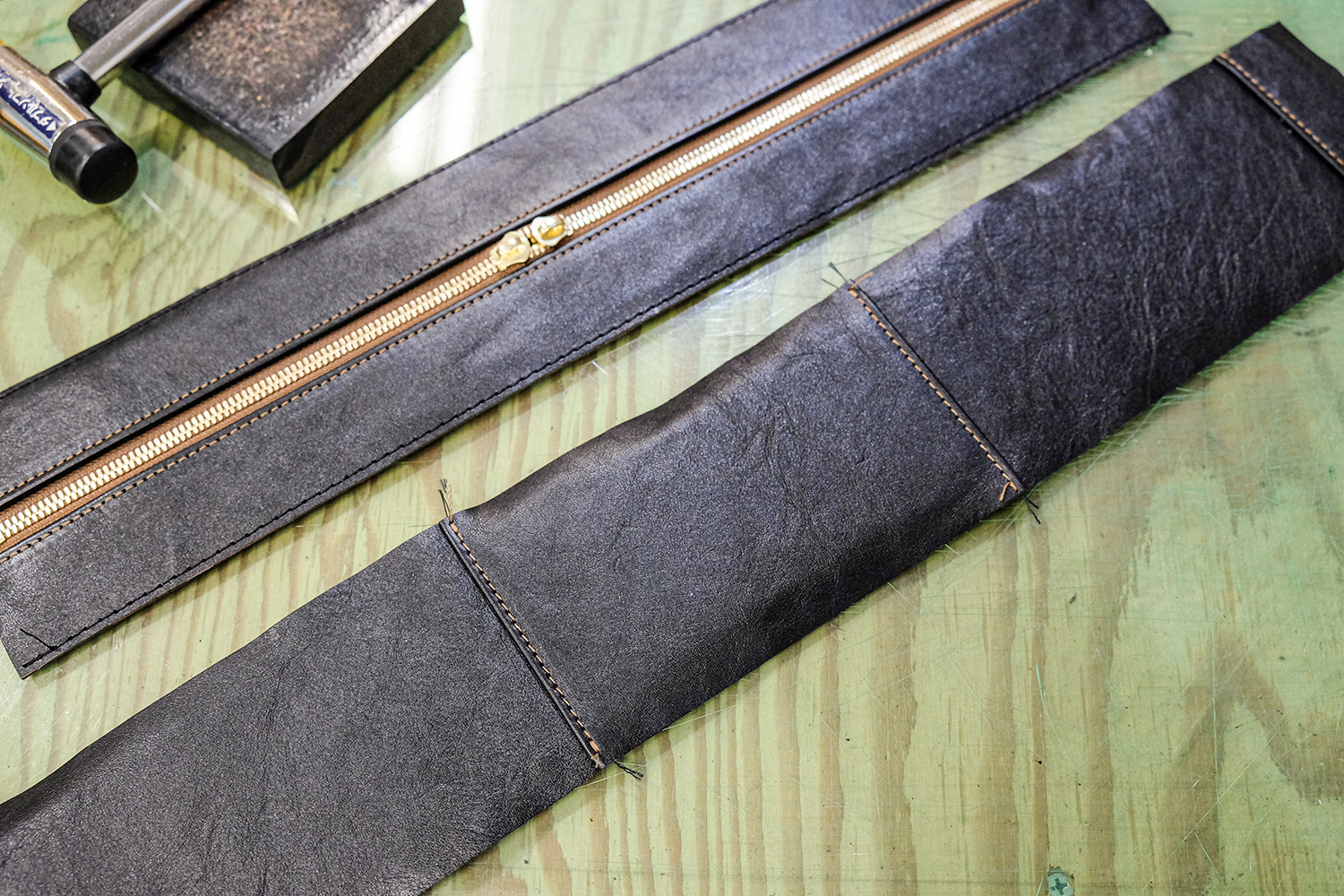
ジッパー部分とボディのボトム&サイド。ジッパーテープは従来モデルと同色。ショートウォレット「OG-9」のジッパー にも採用する茶褐色だ。ボトム&サイドにはすべて芯材を挟み込んでいるが、ボトム中央部分の芯材を従来モデルよりも厚くすることで、よりコシの強いバッグに進化させた。
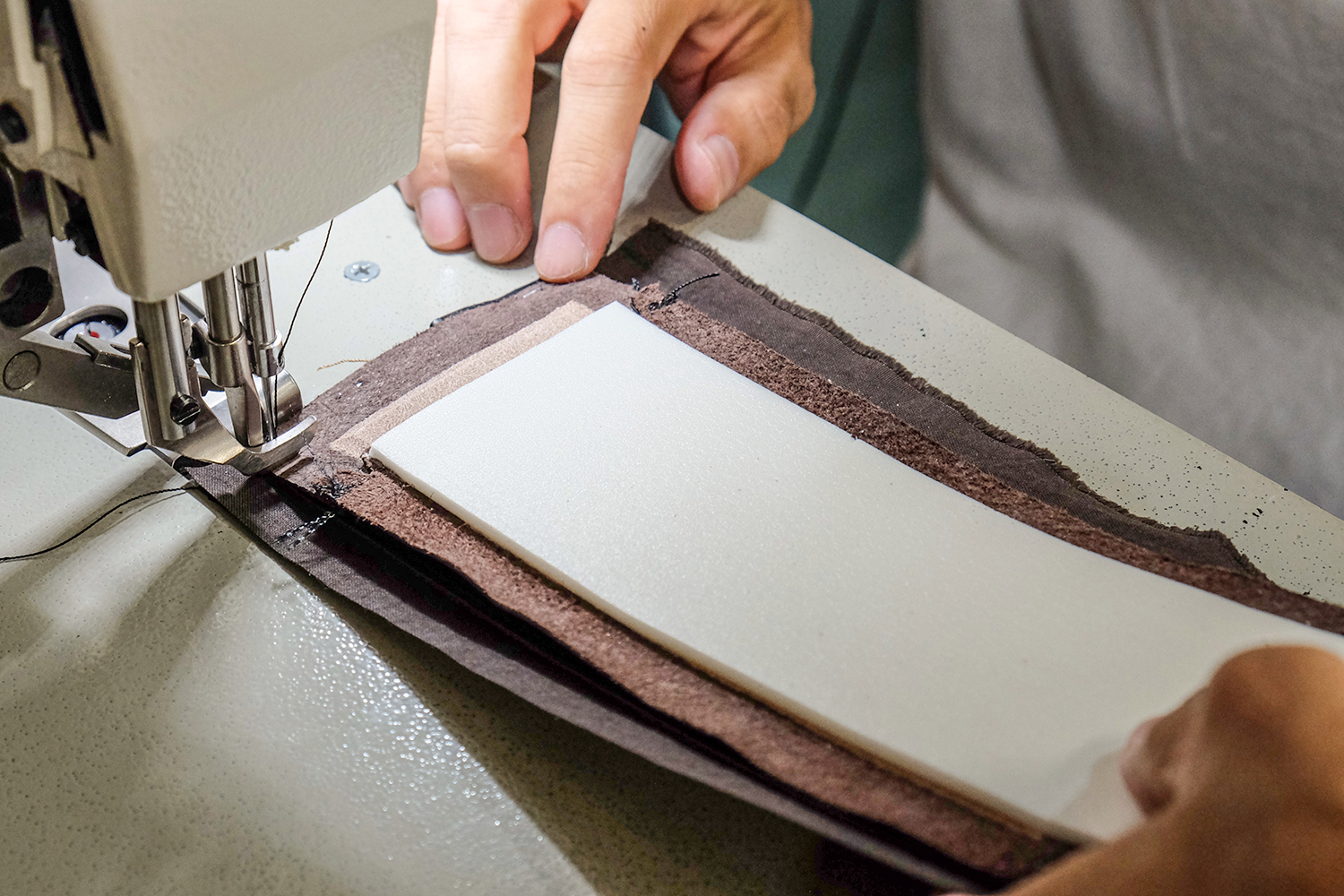

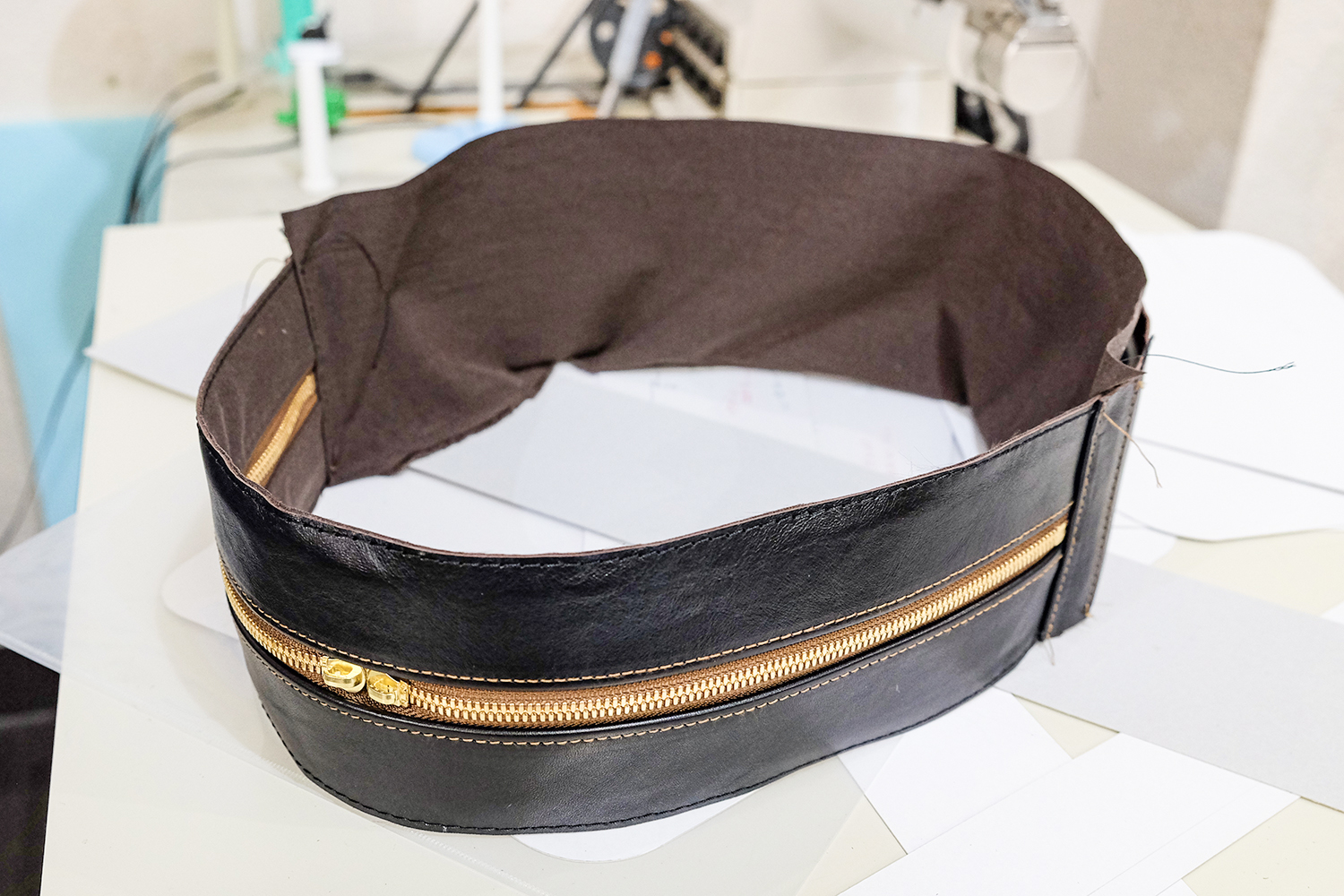
ジッパー部分とボディのボトム&サイドに裏地を装着し、ループ状に縫い合わせる。
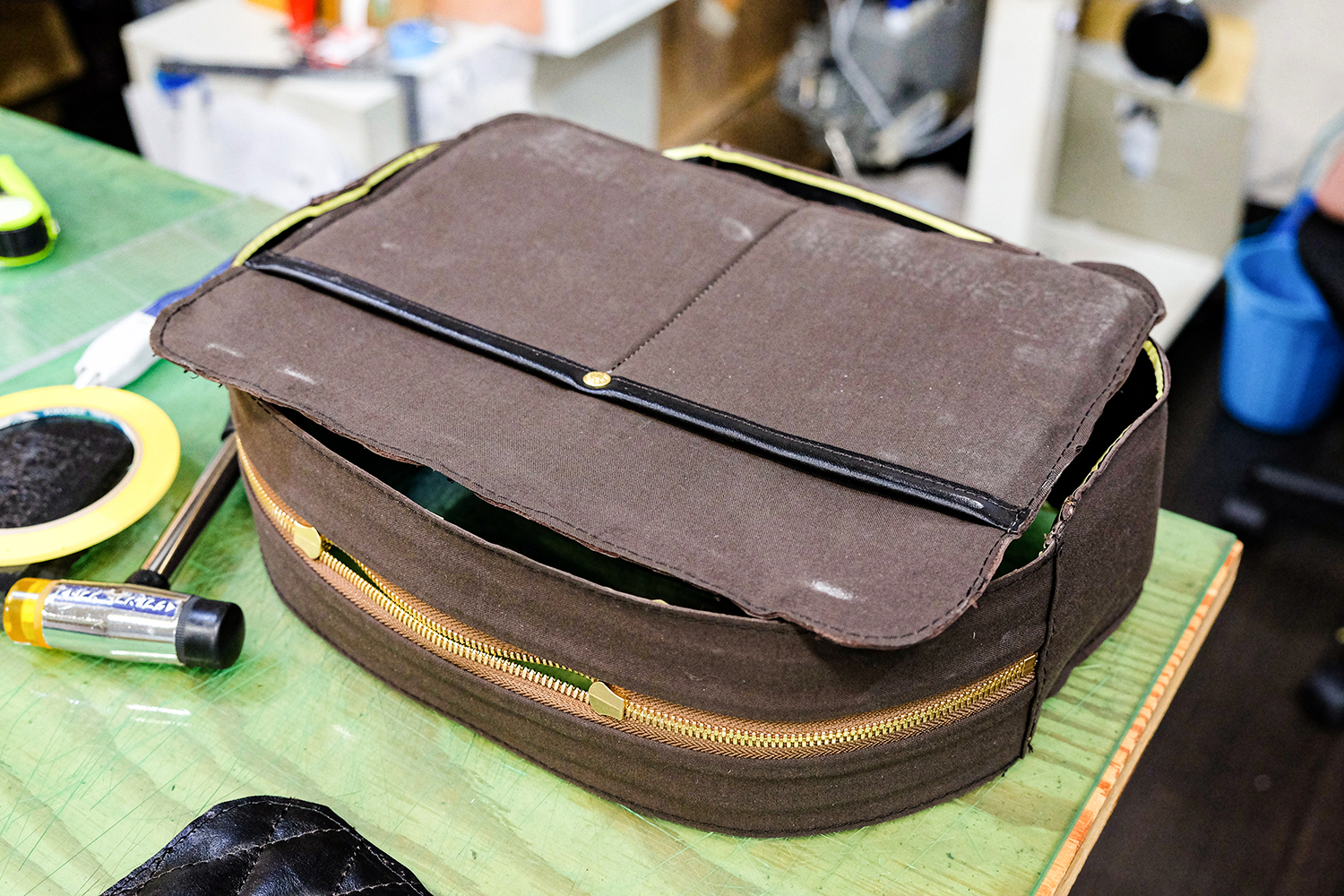
写真のように組み合わせることで、箱状のバッグになる。
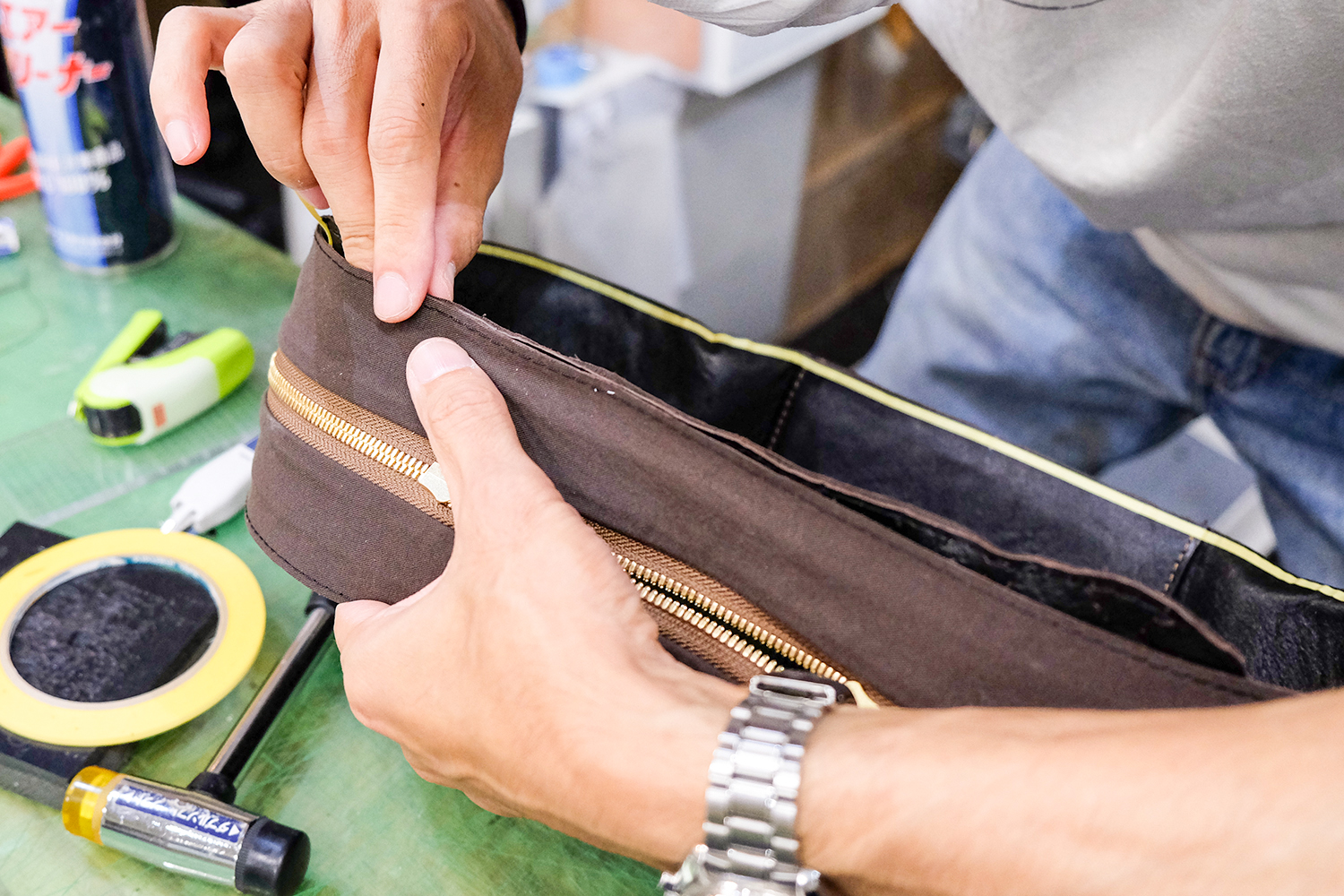
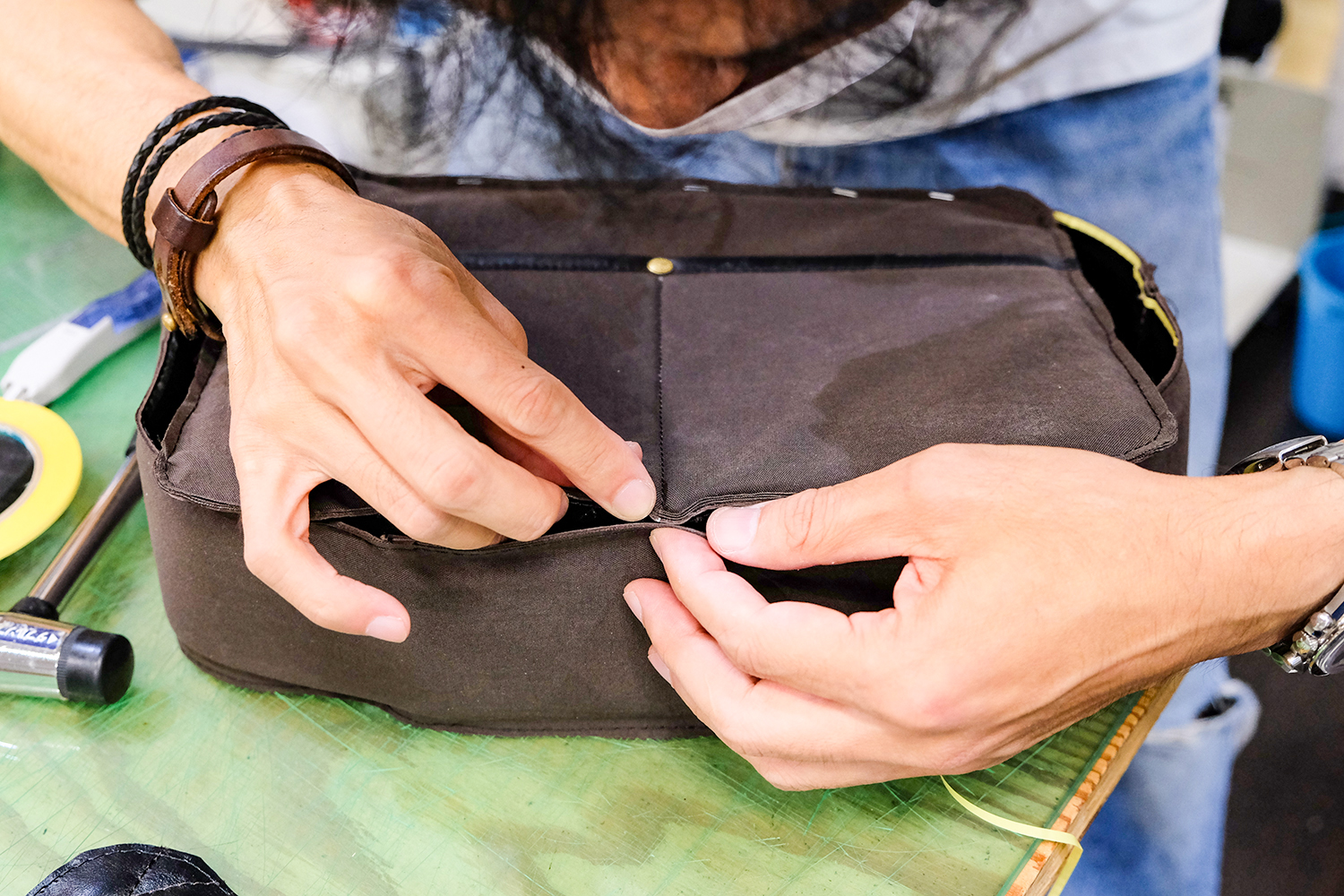
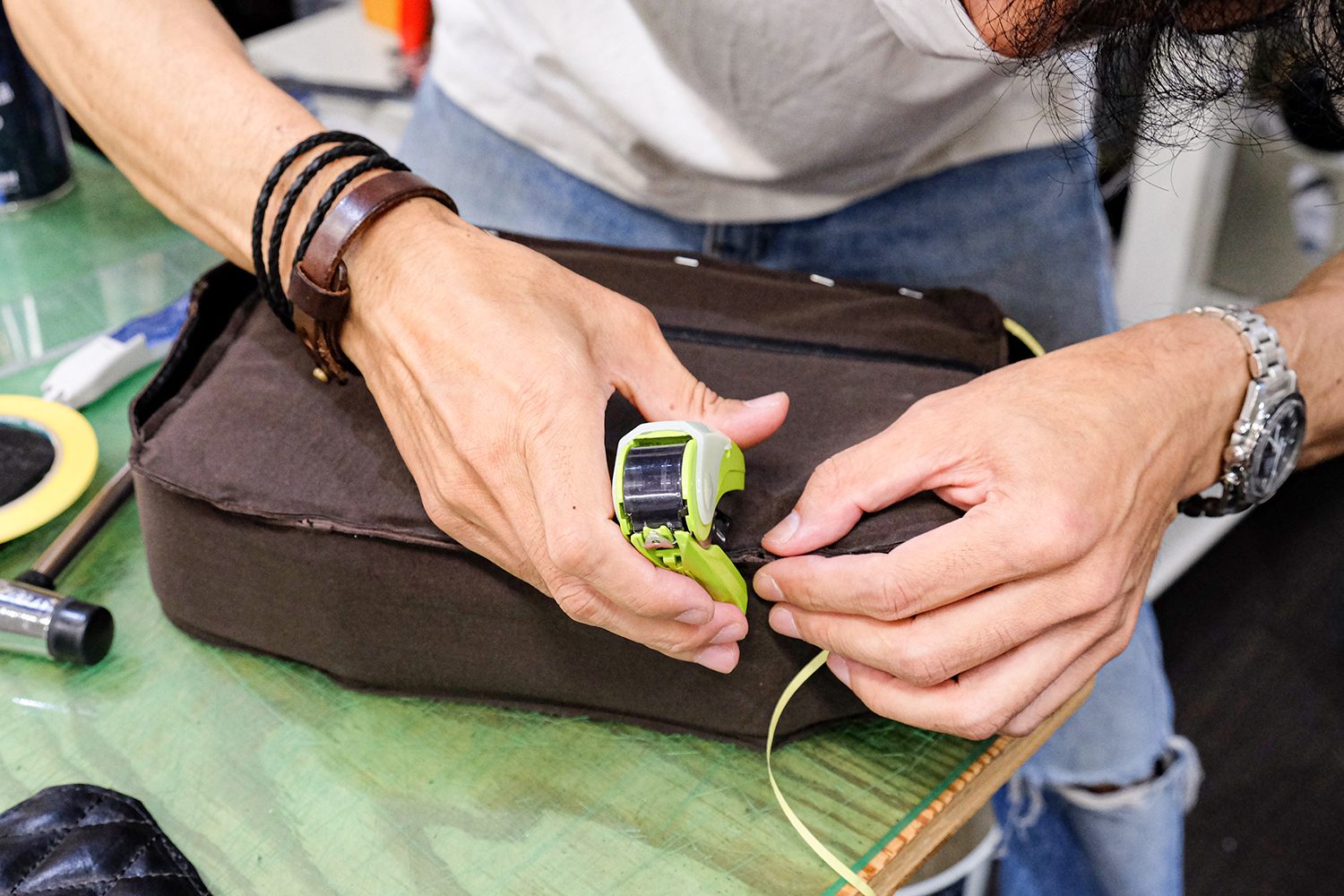
少しでもズレると完成した際に歪んでしうまうので、要所をマーキングして丁寧に両面テープで貼り合わせる。その後、ホチキスで仮止め。
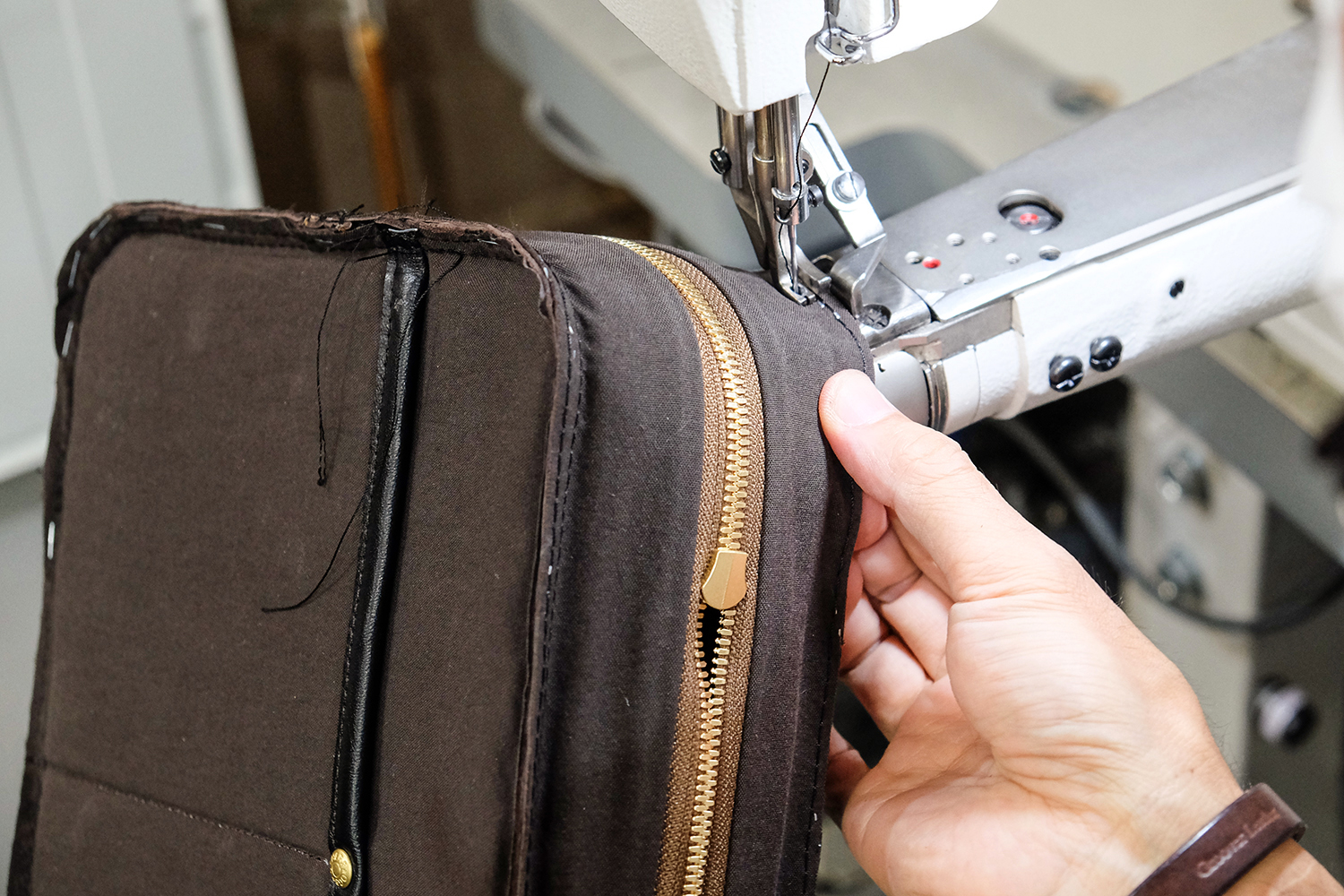
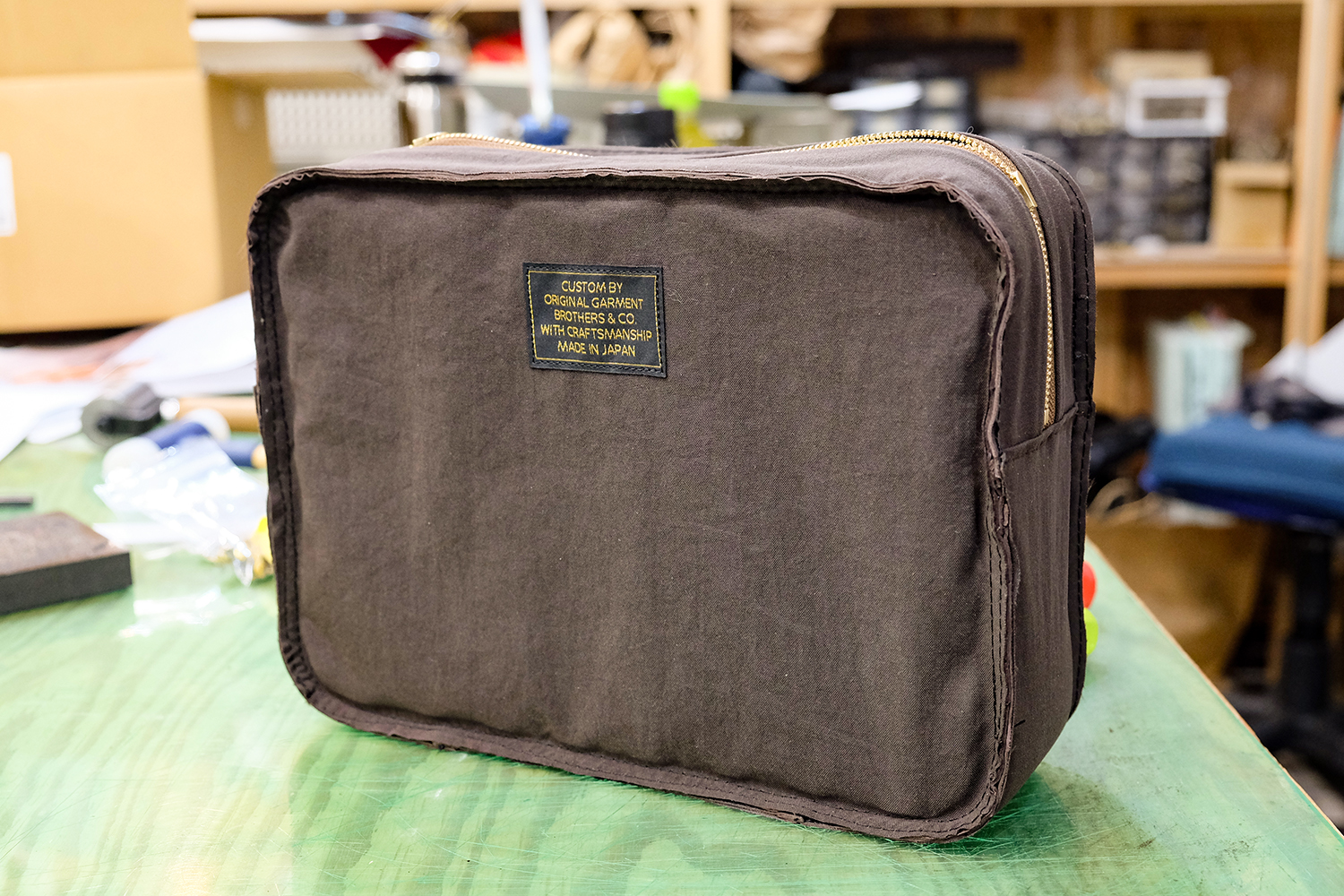
そして箱状に縫い合わせる。朝から始めたサンプル製作だが、この時点で既に遅めの夕方。疲れ切って視点が定まらないオガワとは対照的に、モチベーションがまったく途切れない徳永氏と原山氏。それどころか、時間の経過と共に手捌きが軽やかになっている。恐るべし。
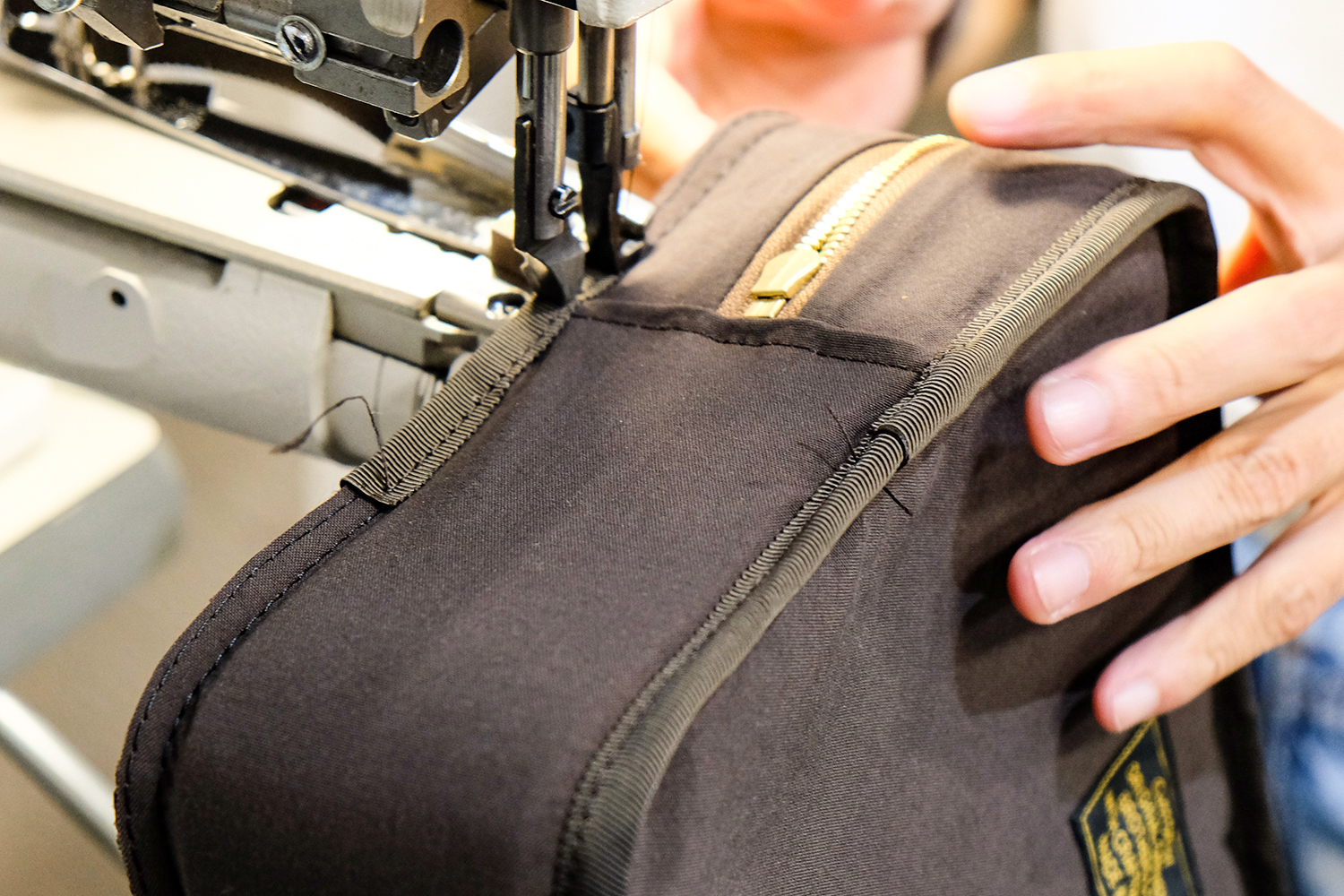
肉厚の生地でパイピングを施して、縫製作業はすべて完了。
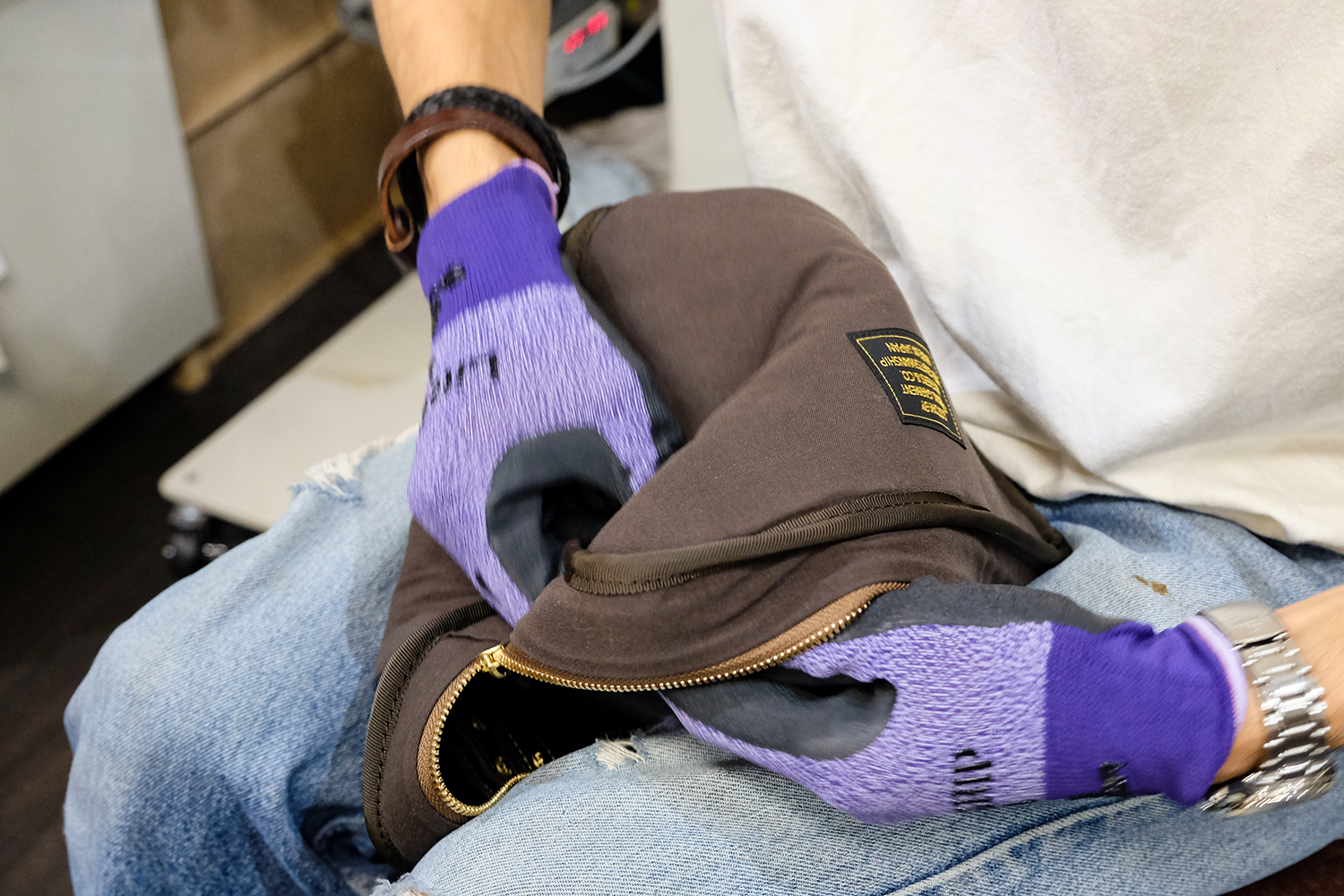
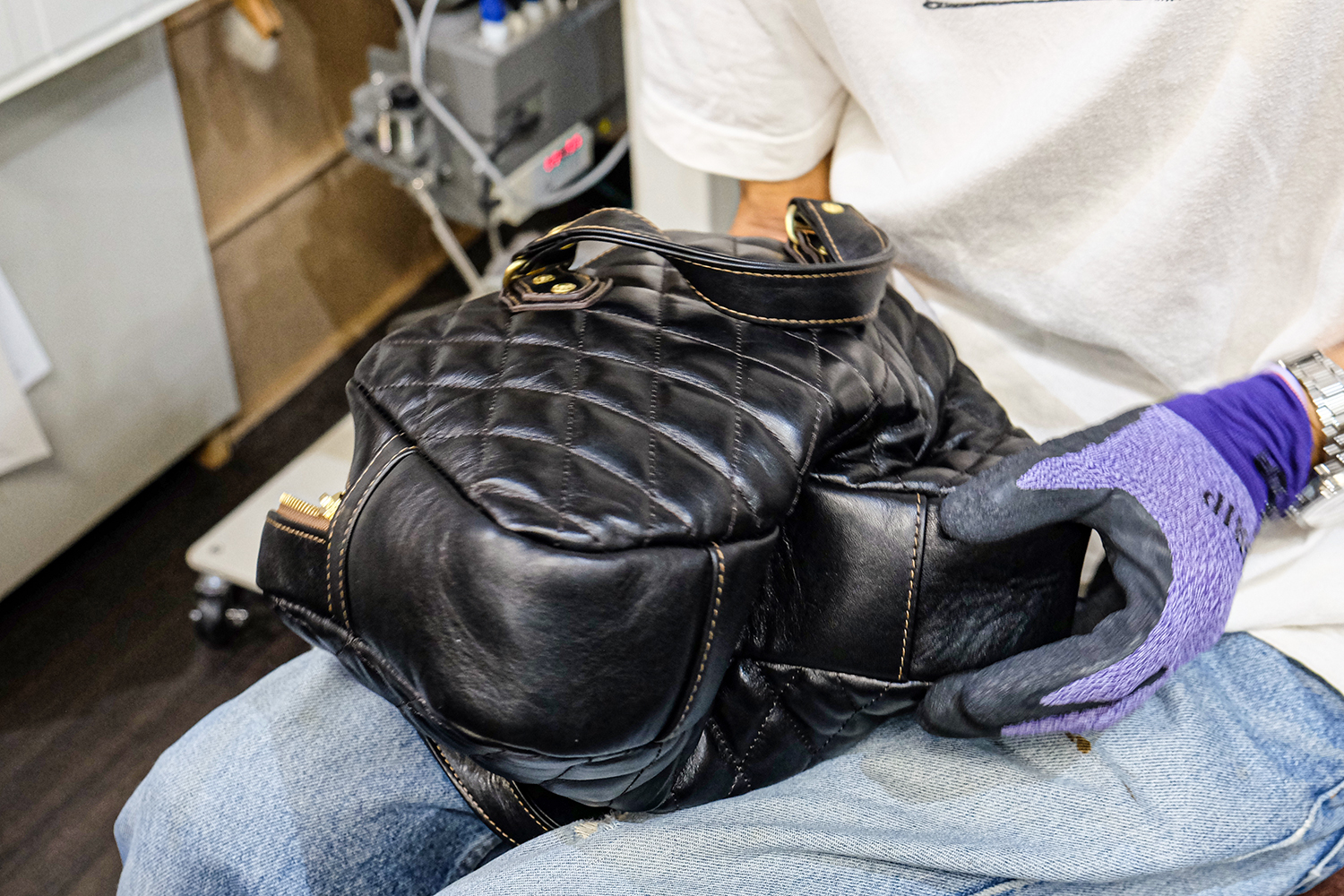
最後の重労働、バッグを表に返す。従来モデルよりもカッチリ感が増したバッグは、表に返すのも一苦労。かなりの力仕事となる。
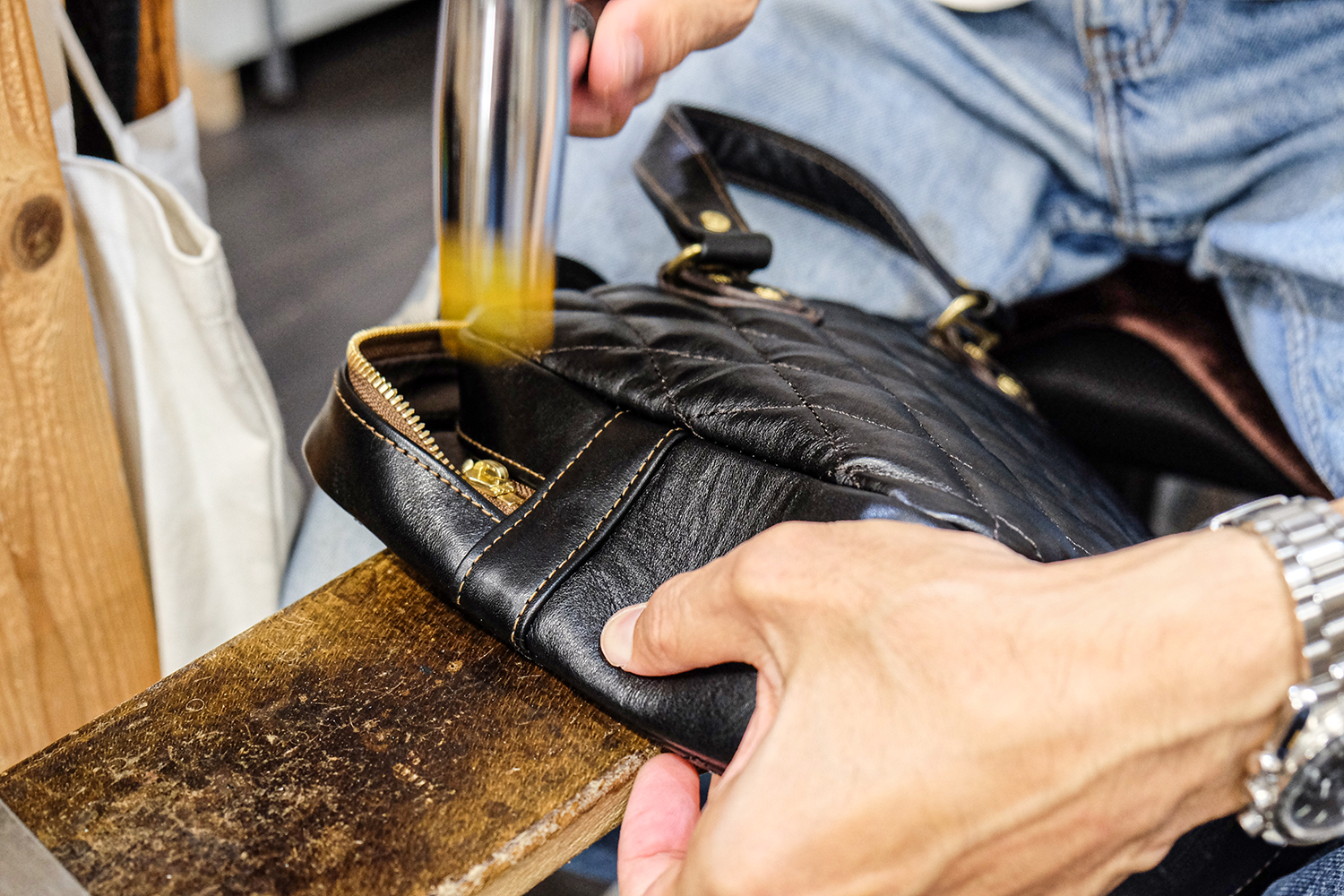

革の折り返し部分をハンマーで叩き、カタチを整えながらクセを付ける。
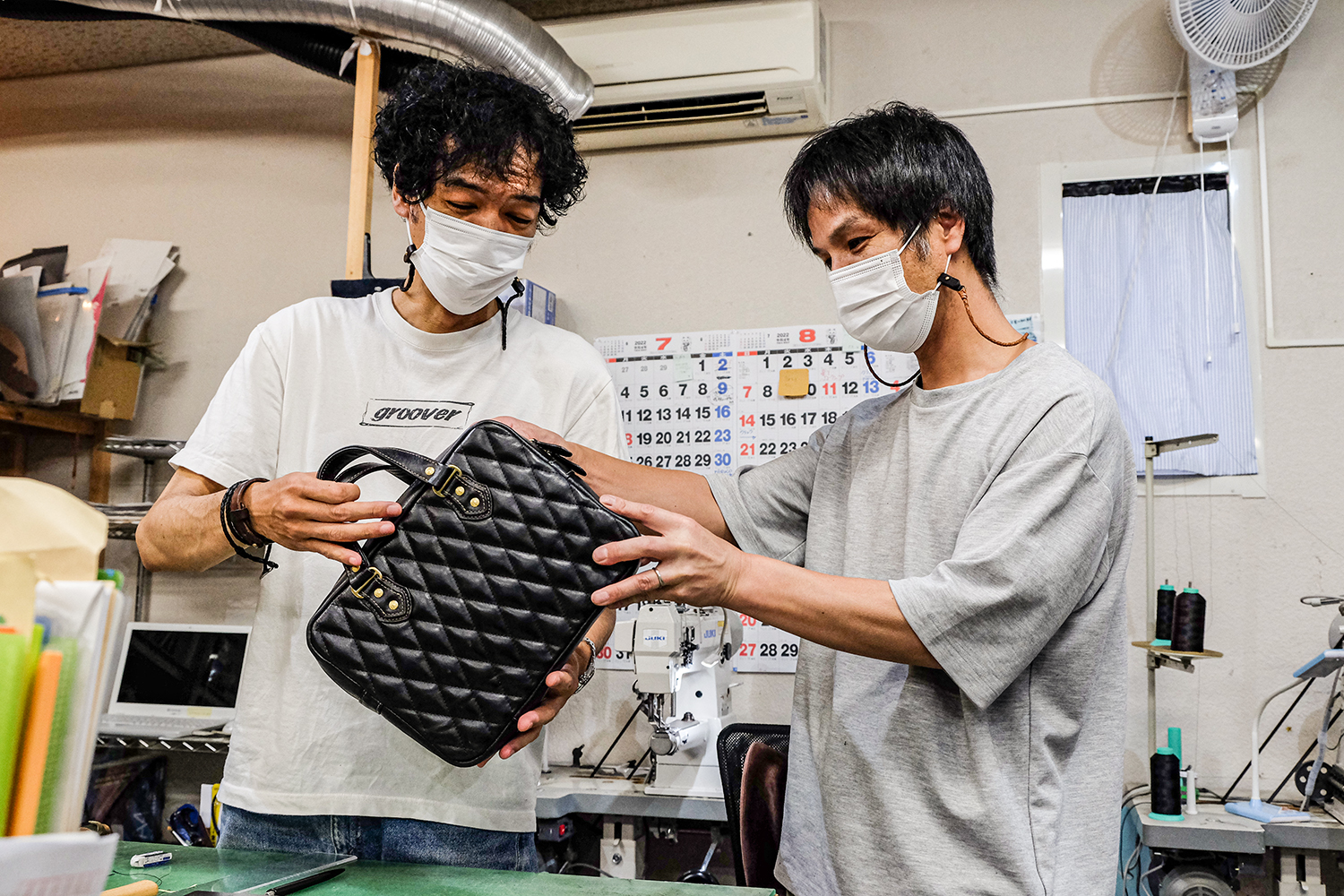
完成した「OG-6」を徳永氏と原山氏が細部まで検証する。サンプルとは修正点、改良点を洗い出すためのプロダクトでもある。気になる箇所はオガワも躊躇せず指摘し、修正をリクエストする。ブラザーに届ける「OG-6」が100%、いや120%の仕上がりになればいいのだ。
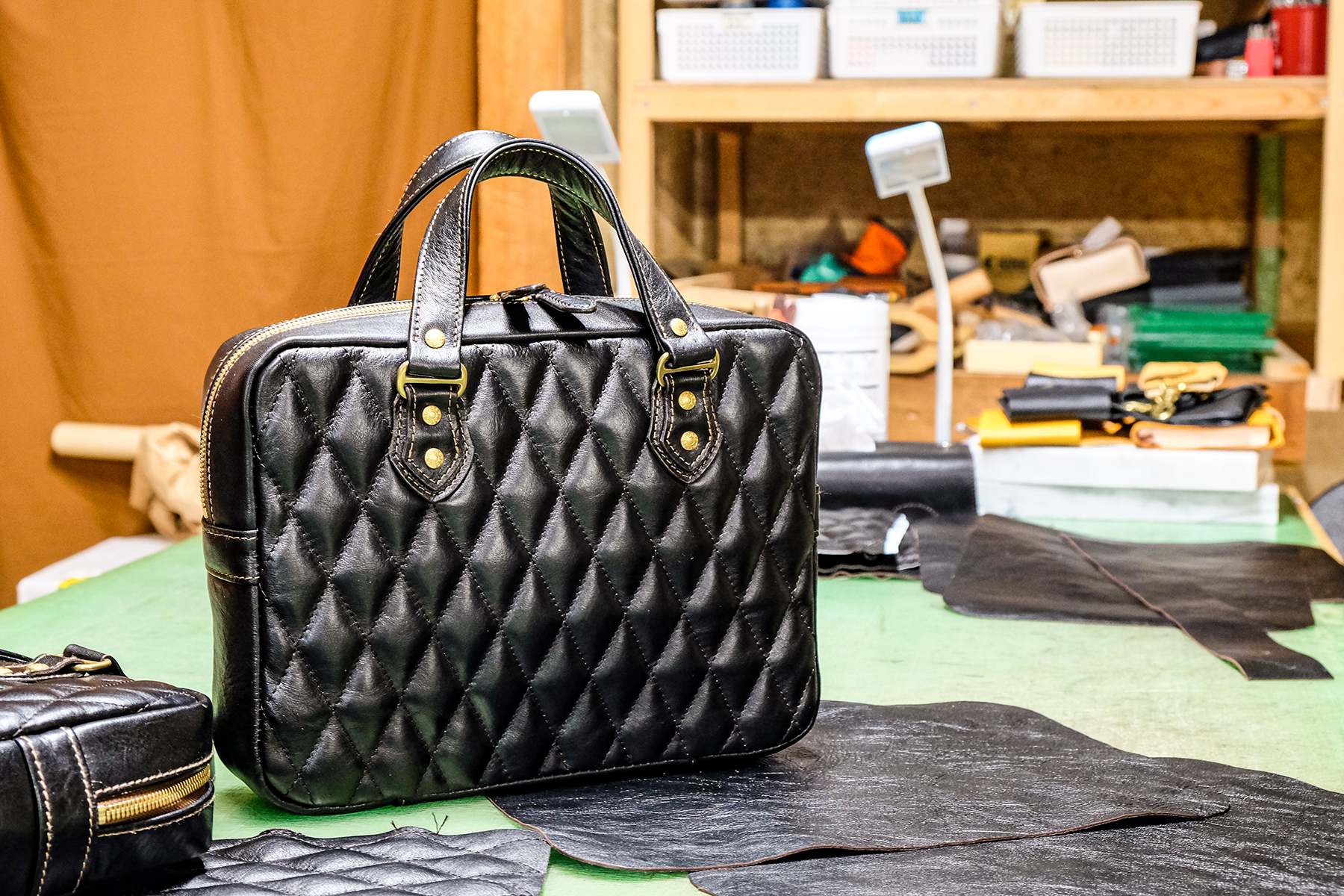
新たな「OG-6」が遂に姿を現した。まだサンプルなので微調整すべき箇所もあるが、質実剛健な仕上がりに大満足。カッチリ感、質感、手触りにこだわった渾身のプロダクト。いよいよオーダー受付開始となる。